Researchers led by a team at UNSW Australia have used the Australian Synchrotron to turn the discovery of an ultra-low density and corrosion-resistant magnesium alloy into the first step toward mass-producing ‘stainless magnesium’, a new high-strength, lightweight metal, paving the way for cars, trucks and aeroplanes that can travel further distances on less petrol.
The magnesium-lithium alloy weighs half as much as aluminium and is 30 per cent lighter than magnesium, making it an attractive candidate to replace these commonly used metals to improve fuel efficiency and greatly reduce greenhouse gas emissions from transport vehicles.
Australian researchers formed a protective surface layer for magnesium that can be considered similar to the way a layer of chromium oxide enables the protection of stainless steel.
‘Many similar alloys have been created as researchers seek to combine the incredible lightness of lithium with the strength and durability of magnesium to develop a new metal that will boost the fuel efficiency and distance capacity of aeroplanes, cars and spacecraft.
‘This is the first magnesium-lithium alloy to stop corrosion from irreversibly eating into the alloy, as the balance of elements interacts with ambient air to form a surface layer which, even if scraped off repeatedly, rapidly reforms to create reliable and durable protection.’
Professor Ferry, senior author of the paper led by Dr Wanqiang Xu also from UNSW, says this excellent corrosion resistance was observed by chance, when his team noticed a heat-treated sample from Chinese aluminium-production giant, CHALCO, sitting, inert, in a beaker of water.
‘To see no corroded surfaces was perplexing and, by partnering with scientists on the Powder Diffraction (PD) beamline at the Australian Synchrotron, we found the alloy contains a unique nanostructure that enables the formation of a protective surface film.
‘Now we’ve turned our attention to investigating the molecular composition of the underlying alloy and the carbonate-rich surface film, to understand how the corrosion process is impeded in this “stainless magnesium”.’
The transport sector accounts for 90 megatonnes (90 billion kilograms) of greenhouse gas emissions in Australia each year, or 16 per cent of Australia’s total; road vehicles account for 77 megatonnes and aviation eight tonnes.
They plan incorporate new techniques into the mass-production of this unique alloy in sheets of varying thickness, in a standard processing plan. Stainless magnesium could be as durable as steel but far lighter.
Nature Materials - A high-specific-strength and corrosion-resistant magnesium alloy
Abstract
Ultra-lightweight alloys with high strength, ductility and corrosion resistance are desirable for applications in the automotive, aerospace, defence, biomedical, sporting and electronic goods sectors. Ductility and corrosion resistance are generally inversely correlated with strength, making it difficult to optimize all three simultaneously. Here we design an ultralow density (1.4 g cm−3) Mg–Li-based alloy that is strong, ductile, and more corrosion resistant than Mg-based alloys reported so far. The alloy is Li-rich and a solute nanostructure within a body-centred cubic matrix is achieved by a series of extrusion, heat-treatment and rolling processes. Corrosion resistance from the environment is believed to occur by a uniform lithium carbonate film in which surface coverage is much greater than in traditional hexagonal close-packed Mg-based alloys, explaining the superior corrosion resistance of the alloy.
Super strong, lightweight metal could build tomorrow's spacecraft
"Our method paves a new way to enhance the performance of many different kinds of metals," said engineer Xiaochun Li.
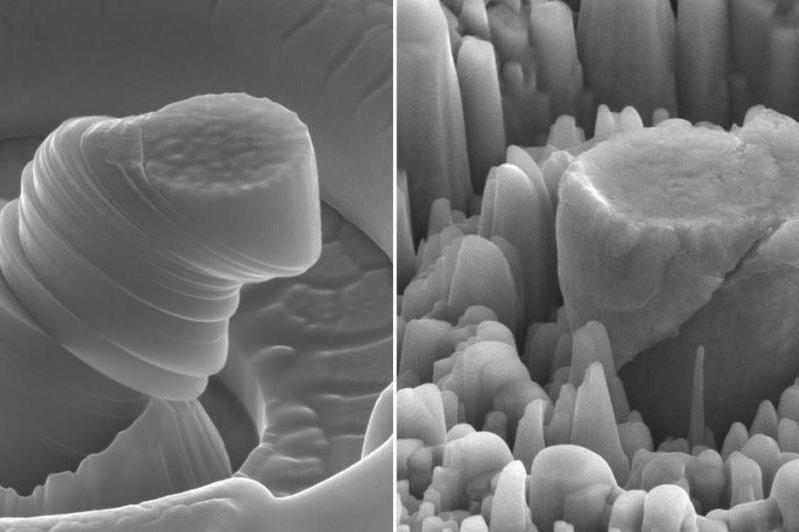
A close-up image shows magnesium before and after the introduction of ceramic nanoparticles. Photo by UCLA/Li
Its inventors, materials scientists at UCLA, say the metal is super strong, but most importantly, lightweight. The metal's stiffness-to-weight ratio is what sets it apart from similar inventions.
Researchers say the metal may be just the first of many groundbreaking manufacturing materials. That's because they've invented a new technique for infusing metals without nanoparticles without hurting the metal's structural integrity.
"It's been proposed that nanoparticles could really enhance the strength of metals without damaging their plasticity, especially light metals like magnesium, but no groups have been able to disperse ceramic nanoparticles in molten metals until now," researcher Xiaochun Li, a professor of manufacturing and engineering at UCLA, said in a press release.
"With an infusion of physics and materials processing, our method paves a new way to enhance the performance of many different kinds of metals by evenly infusing dense nanoparticles to enhance the performance of metals to meet energy and sustainability challenges in today's society."
After processing, researchers tested the magnesium, newly infused with a dense, even spread of nanoparticles. The new material showed improved strength, stiffness, plasticity and durability under high temperatures.
Previous research showed ceramic nanoparticles have a tendency to clump together when added to metals, making them stronger but weakening their plasticity. Researchers solved this problem by dispersing the nanoparticles in a molten magnesium zinc alloy.
Because magnesium is relatively abundant and the production technology can be easily scaled up, scientists hope the metal's industrial applications will be quickly realized. And scientists don't think it will be long before they've found a new metal-nanoparticle combination with impressive potential.
"The results we obtained so far are just scratching the surface of the hidden treasure for a new class of metals with revolutionary properties and functionalities," Li said.
The new metal nanocomposite is detailed in the jouranl Nature.
No comments:
Post a Comment