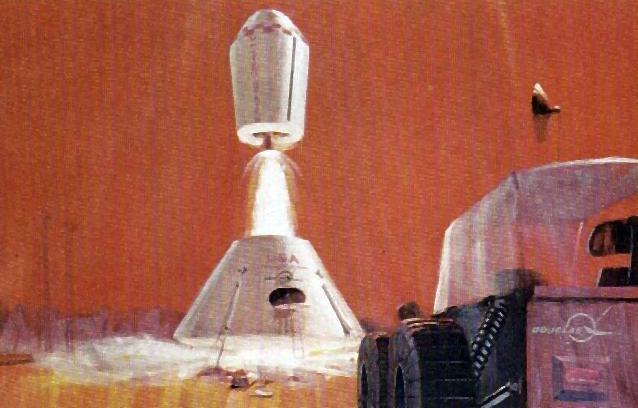
Deimos Departure Credit: NASA deimos2.jpg. Deimos - MEM Descent Credit: NASA
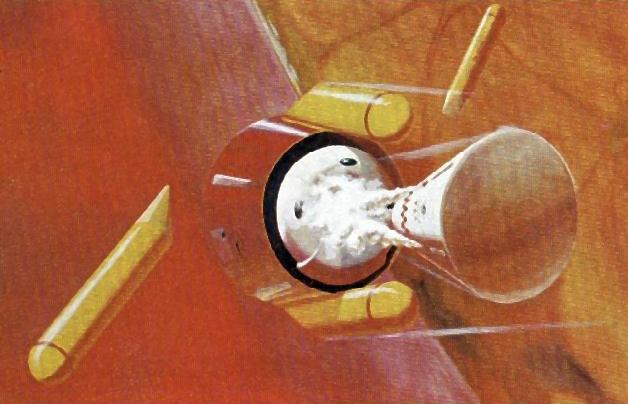
Deimos Departure Credit: NASA deimos2.jpg. Deimos - MEM Descent Credit: NASA

Gemini-SASSTO dimensions and cutaway (Lowther, "Reusable Saturns," p.24)
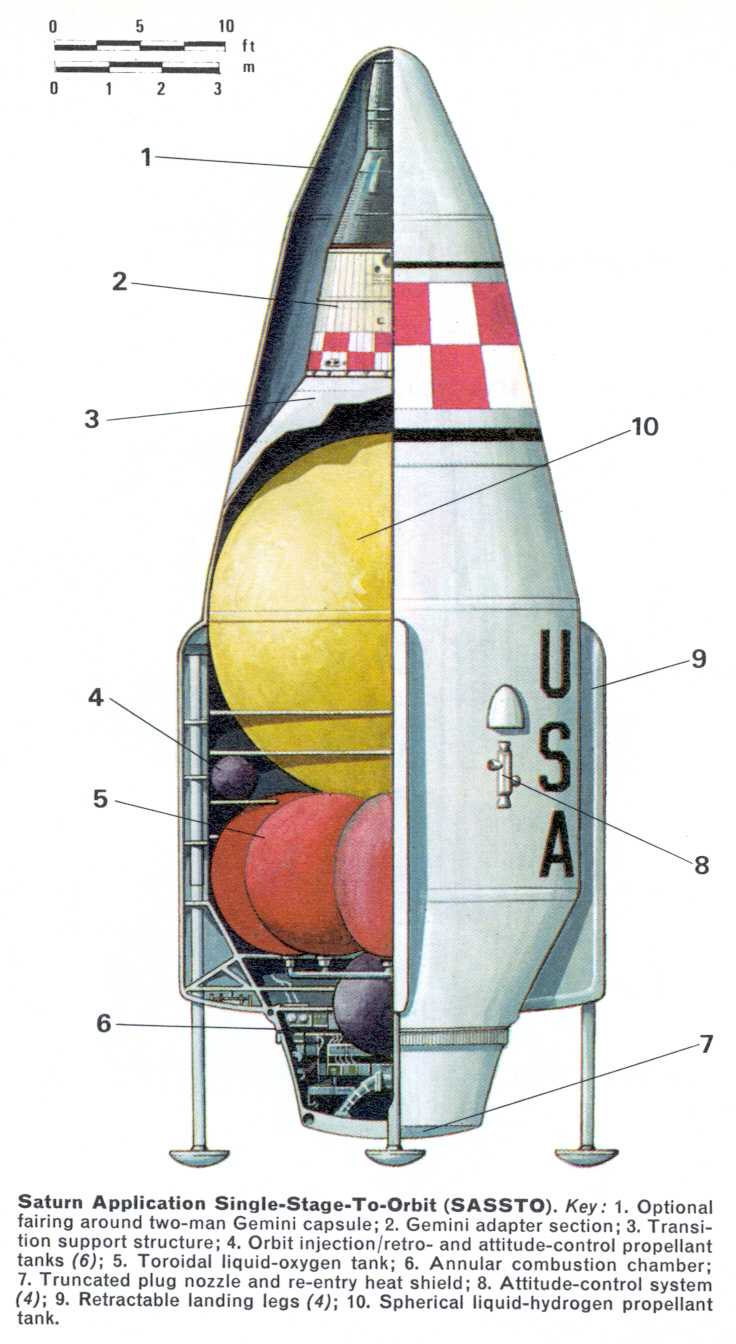
Gemini-SASSTO dimensions and cutaway (Lowther, "Reusable Saturns," p.24)


Frontiers of Space The Pocket Encyclopedia Of Spaceflight In Color
by Philip Bono and Kenneth Gatland Published 1969
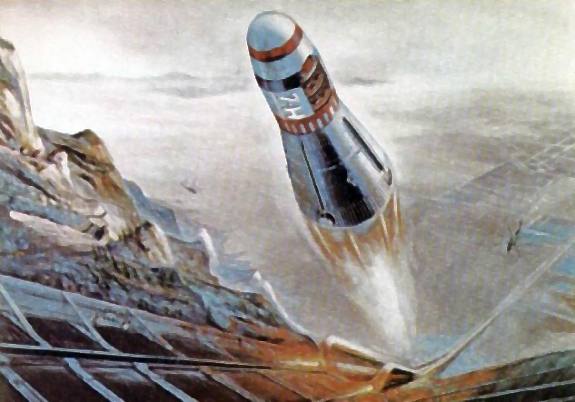
yperion Single Stage To Orbit (Philip Bono)

Douglas also proposed a military VTVL SSTO for transporting troops and cargo
the ”Ithacus.” The Ithacus plan was apparently inspired by general Wallace M. Greene,

ITHACUS VTVL SSTO Troop Carrier
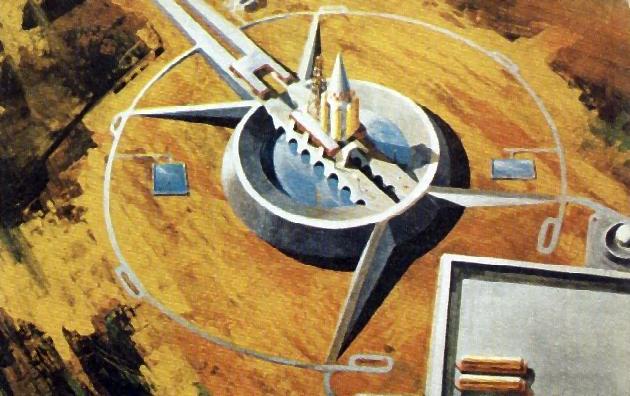
Rombus


Ithacus.jpg - Wikimedia Commons


Philip Bono
From Wikipedia, the free encyclopedia
Philip Bono (13 January 1921 – 23 May 1993) was a Douglas Aircraft Company engineer. He was a pioneer of reusable vertical landing single-stage to orbit launch vehicles.Bono pursued single-stage space launch as simpler and cheaper. He realized to do this he would need to use high specific impulse liquid hydrogen/liquid oxygen rocket engines. Afterwards he proposed to make these vehicles reusable. From his ROOST design onwards Bono advocated space launch vehicles without wings, usually using rocket assisted vertical takeoff and landing (VTVL). According to his estimates, wings consisted mostly of dead weight that decreased launch payload mass. He patented a reusable plug nozzle rocket engine which had dual use as a heat shield for atmospheric reentry. His early 1960s concepts influenced later designs like the 1990s Delta Clipper, also from Douglas.
Birth, education and career
Philip Bono was born in Brooklyn, New York on 13 January 1921.[1] He graduated from the University of Southern California in 1947 with a degree in mechanical engineering. After graduation, Bono worked as a research and systems analyst for North American Aviation. Bono began working for Douglas Aircraft company in 1960. After the merger of McDonnell Aircraft and the Douglas Aircraft Company, he worked for McDonnell Douglas Astronautics from 1966 until 1988. Philip Bono died on 23 May 1993 at the age of 72. He was a resident of Costa Mesa, California at the time of his death.[2]Less than three months after Bono's death, the first launch vehicle based on his designs, the McDonnell Douglas DC-X (Delta Clipper) began a largely successful series of test flights. The DC-X was a vertical-takeoff and vertical landing vehicle. The series of test flights began on 18 August 1993 and continued until the launch vehicle was damaged on landing on 16 May 1995.[3]
Designs
- One Stage Orbital Space Truck (OOST) [4]
- Recoverable One Stage Orbital Space Truck (ROOST) [5]
- Reusable Orbital Module, Booster, and Utility Shuttle (ROMBUS)[6][7]
- Ithacus[8][9]
- Pegasus [10]
- Hyperion[citation needed]
- SASSTO [11]
Bibliography
Philip Bono & Kenneth William Gatland, Frontiers Of Space, ISBN 0-7137-3504-XDouglas SASSTO
From Wikipedia, the free encyclopedia
Douglas Aircraft's SASSTO, short for "Saturn Application Single Stage to Orbit", was a single-stage-to-orbit (SSTO) reusable launch system designed by Philip Bono's team in 1967. SASSTO was a study in minimalist designs, a launcher with the specific intent of repeatedly placing a Gemini capsule in orbit for the lowest possible cost. The SASSTO booster was based on the layout of the S-IVB upper stage from the Saturn family, modified with a plug nozzle.
Although the SASSTO design was never followed up at Douglas, it is
widely referred to in newer studies for SSTO launchers, notably the MBB "Beta" design, which was largely an updated version of SASSTO.Contents
History
In 1962 NASA sent out a series of studies on post-Apollo launch needs, which generally assumed very large launchers for a manned mission to Mars. At Douglas, makers of the S-IVB, Philip Bono led a team that studied a number of very large liquid-fueled boosters as a way to lower the cost of space exploration. His designs were based on an economy of scale which makes larger rockets more economical than smaller ones as the structure accounts for less and less of the overall weight of the launcher.[1] At some point the dry weight of the launcher becomes lower than the payload it can launch, after which increases in payload fraction are essentially free. However, this point is crossed at relatively large vehicle sizes - Bono's original OOST study from 1963 was over 500 feet (150 m) long - and this path to lower costs only makes sense if there is an enormous amount of payload that needs to be launched.After designing a number of such vehicles, including ROOST and the ROMBUS/Ithacus/Pegasus series, Bono noticed that the S-IVB stage, then just starting to be used operationally, was very close to being able to reach orbit on its own if launched from the ground. Intrigued, Bono started looking at what missions a small S-IVB-based SSTO could accomplish, realizing that it would be able to launch a manned Gemini capsule if it was equipped with some upgrades, notably an aerospike engine that would improve the specific impulse and provide altitude compensation.[2] He called the design "SASSTO", short for "Saturn Application Single-Stage To Orbit".
These same upgrades would also have the side-effect of lowering the weight of the SASSTO compared to the original S-IVB, while at the same time increasing its performance. Thus the study also outlined a number of ways that it could be used in place of the S-IV in existing Saturn IB and Saturn V stacks, increasing their performance. When used with the existing Saturn I lower stage, it would improve payload to low earth orbit from 35,000 to 52,500 lb (23,800 kg), or 57,000 lb (26,000 kg) if the landing gear were removed and it was expended like the S-IVB. SASSTO would thus give NASA a short-term inexpensive manned launch capability, while also offering improved heavy-launch capability on the existing Saturn infrastructure.
SASSTO required a number of new technologies, however, which made development risky. In particular, the performance of the aerospike engine had to be considerably higher than the J-2 it would replace, yet also offer the ability to be restarted multiple times as the single engine was used for launch, de-orbit and landing. Of particular note was the final landing burn, which required the engines to be restarted at 2,500 ft (760 m) during the descent. The vehicle's weight was also greatly reduced, almost by half, which would not have been trivial considering the relatively good performance of the S-IVB design.
Design
Although the SASSTO claimed the S-IVB as its starting point, this was a conceit, and the vehicle had little in common with the S-IVB except its size.The internal fuel tankage was considerably different than in the S-IV. The LH2 was no longer cylindrical, but spherical, and moved to the forward location in the fuselage. The LOX tankage, originally on top of the LH2, was re-positioned into a series of smaller spherical tanks arranged in a ring below the LH2. The tanks were all moved forward within the airframe compared to the engine, all of these changes being made in order to reduce changes in the center of gravity as the fuel was burned off. The fuselage section immediately above the engine was necked down, forming what appeared to be a larger single plug. The upper section of the fuselage, over the top of the hydrogen tank, was likewise necked down.
In order to increase the amount of LH2 being carried, given the fixed dimensions, SASSTO proposed freezing 50% of the fuel to produce a slush hydrogen mixture. This improvement was not uncommon in designs of the era, although it was not until the 1990s that any serious development work on the concept was carried out.[3]
The rearmost portion of the spacecraft was a single large plug nozzle, fed by a series of 36 injectors operating at 1500 psia, producing 277,000 lbf (1,230 kN) of thrust. Since plug nozzles gain efficiency as they grow larger, the 465 sec specific impulse (compared to the J-2's 425) was not particularly aggressive. The engine also served as the primary heat shield, actively cooled by liquid hydrogen that was then dumped overboard.
Four landing legs extended from fairings on the fuselage sides, retracting to a point about even with the "active" portion of the engine area. Four clusters of small maneuvering engines were located between the legs, about half-way from front to back along the fuselage. A series of six smaller tanks arranged in the gaps between the LOX and LH2 tanks fed the maneuvering engines.
SASSTO delivered 6,200 lb (2,800 kg) of cargo to a 110 nmi (200 km) orbit when launched due east from the Kennedy Space Center. Empty weight was 14,700 lb (6,700 kg), considerably lighter than the S-IVB's 28,500 lb (12,900 kg), and gross lift off weight was 216,000 lb (98,000 kg). The typical payload was the Gemini, which was covered with a large aerodynamic fairing.
Re-entry maneuverability was through a blunt-body lifting profile, similar to the Apollo CSM. The cross-range was limited, about 230 miles (370 km), and there was basically no maneuverability at all on final approach. There was enough fuel for about 10 seconds of hovering and small maneuvers to select a flat landing spot. Because SASSTO was the same basic size as the S-IVB, Douglas proposed transporting it in the existing Aero Spacelines Super Guppy after landing at either Wendover Air Force Base in Utah, or Fort Bliss outside El Paso, Texas.
Developments
Dietrich Koelle used SASSTO as the starting point for a similar development at Messerschmitt-Bölkow-Blohm in the late 1960s. Unlike Bono's version, Koelle used as much existing technology and materials as possible, while abandoning the need for the specific S-IVB sizing. The result was a slightly larger spacecraft, the Beta, that launched 4,000 lb (1,800 kg) of payload without the use of slush fuel, advanced lightweight construction, or a real aerospike engine. As part of the Beta proposal, Koelle pointed out that even the existing S-IVB could reach orbit, with zero payload, if equipped with a high-pressure LOX/LH2 engine of 460 Isp.[4]Gary Hudson later pointed out that such an engine existed, the Space Shuttle Main Engine, using a SSME-powered S-IVB as a thought experiment to demonstrate the real-world feasibility of SSTO launchers.[5] This study was part of his "Phoenix" series of launchers, all similar to the SASSTO.[6]
Encyclopedia Astronautica
SASSTO
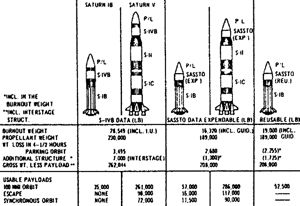
SASSTO Comparison
Credit: NASA
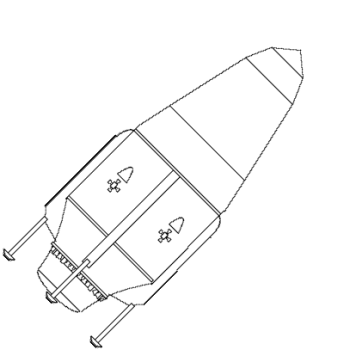
SASSTO
SASSTO - Saturn-derived SSTO Launch Vehicle
Credit: © Mark Wade
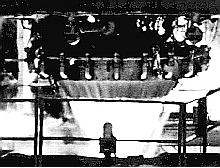
Plug nozzle test
Plug nozzle test, ca. 1968
Credit: NASA
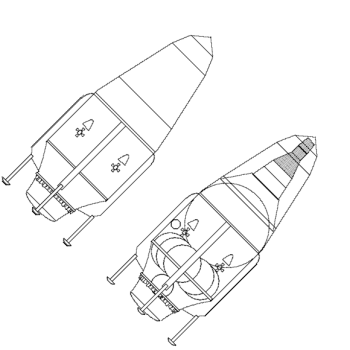
SASSTO
SASSTO - Saturn-derived SSTO Cutaway
Credit: © Mark Wade
The resulting vehicle became known as "Saturn Application Single Stage to Orbit". Notable design features included an aft-mounted liquid oxygen tank to reduce the difference between vehicle centre of gravity and centre of aerodynamic pressure, and a hydrogen cooling system for the main engine to provide thermal protection during re-entry. Thermal analysis indicated that although the engine itself would be adequately protected by this system, the areas located above the exhaust nozzles would not. Consequently, the designers had to resort to an ablative, expendable material (200 kilograms of Armstrong Insulcork 2760) bonded to the aluminium structure although it would increase the maintenance cost.
The oxygen/hydrogen mixture ratio was 6:1 rather than 7:1 since the designers felt a high oxygen ratio would degrade the exhaust velocity and payload capability. 50% hydrogen slush was used to reduce the volume of the fuel tank. The 36-segment plug nozzle propulsion system would have operated at a pressure of 1500psia. It would be used for ascent, orbit insertion, de-orbit and (beginning at an altitude of 760 meters-) the final landing burn. The vehicle would carry enough propellant for hovering for 10 seconds before landing at an unprepared site, if necessary. The estimated landing accuracy of 1853 * 3700 m was not regarded as a major concern since the Gemini 6-12 flights achieved an average touchdown dispersion of only 6.85km although the capsule had essentially no manoeuvring capability below 30.5km altitude. The re-entry cross range capability was about +-370km, permitting a safe landing at El Paso, TX or Wendover Range, UT after 2-3 orbits from Cape Canaveral. Wendover was the preferred emergency landing site since SASSTO easily could have been returned from nearby Hill AFB to Cape Canaveral in a "Pregnant Guppy" S-IV-B transport aircraft.
SASSTO had a payload capability of 3,629kg to a 185km orbit and the standard payload would be a 2-man Gemini spacecraft protected by a jettisonable fairing to reduce drag losses during ascent. This would provide a safe emergency escape system for the test pilots, and the Gemini ejection seats, heatshield, parachutes etc. (1542kg in all) could later be removed as the flight test program increases confidence in SASSTO reliability. Douglas envisioned this vehicle as a "space fighter" capable of satellite inspection missions, or space station resupply flights lasting a maximum of 48 hours. It could also deliver 2,812kg of liquid hydrogen to a spacecraft in Earth orbit.
Since SASSTO was loosely based on the Saturn S-IV-B rocket stage, Douglas also proposed an expendable version for use as a more capable upper stage with the Saturn IB and Saturn V launch vehicles. The expendable SASSTO stage would have had a burnout mass of 7,400kg and carried 85,729kg of oxygen+hydrogen propellant. The stage was thus of a much more lightweight construction than the standard S-IV-B (12,949kg + 104,326kg LOX,LH2) and the new aerospike engine would have been more efficient as well (464s specific impulse vs. 426s for the J-2 engine). Consequently, the Saturn V's payload capability would have been boosted by 8-11t as well. The Saturn IB's basic 15876-kilogram payload capability to a 185km orbit would have increased to 23814-25855kg depending on whether SASSTO would be flown in expendable or reusable mode. The latter version was known as SARRA (Saturn Application Retrieval and Rescue Apparatus) and was intended for returning stranded Apollo crews from the lunar surface.
Finally, the Douglas design team also compared the cost of SASSTO with two different all-rocket VTHL TSTOs: a winged 1st stage plus lifting-body 2nd stage (centre) and winged first and second stages (right). All three vehicles were designed for a 2,812-kilogram payload although the lifting-body TSTO only was able to carry 2,086kg due to centre of gravity problems. No attempt was made to estimate the marginal launch cost since there were too many unknown factors. VTVL SSTO would however be expected to yield a significant operational advantage since only a single vehicle must be maintained and the VTVL SSTO does not require a landing runway. SASSTO was expected to cost $1.1. billion to develop (=$5.88B at 1999 rates). The winged VTHL TSTO would cost 2.2 times as much to develop as SASSTO while the smaller lifting-body TSTO variant would be 50% more expensive. The winged and lifting-body 1st unit production costs would be 4 and 2.7 times higher than the SASSTO 1st unit cost, respectively.
The general conclusion was that the complex winged or lifting-body TSTO shapes result in added lift-off and manufactured weights of a more expensive construction than ballistic wingless SSTOs. For example, the lifting-body TSTO dry mass (12,274kg + 2,086kg payload) is 2.4 times higher, and the winged TSTO weighs 3.6 times as much (18,176kg+2,812kg P/L) as SASSTO at touchdown. The gross lift-off weights bear the relationships of 1.0 (SASSTO; 97,887kg GLOW), 1.25 (lifting body orbiter TSTO; 122,245kg GLOW) and 1.91 (wing-body orbiter TSTO; 187,020kg GLOW). In that case, is the combination of lower re-entry g-loads, better manoeuvrability (landing go-around with jet engines) and improved cross range really worth the cost of carrying wings...?
Although TSTO thus appears to be uncompetitive vs. ballistic single-stage RLVs for small payloads, the authors admit that requirements for higher payloads (22.68-45.6t) may yield rapid increases in propellant mass fraction for winged two-stage vehicles, making TSTO more performance/cost-effective.
LEO Payload: 2,812 kg (6,199 lb) to a 185 km orbit at 28.00 degrees. Development Cost $: 1,100.000 million. Launch Price $: 0.030 million in 1968 dollars. Flyaway Unit Cost $: 16.100 million in 1968 dollars in 1968 dollars.
Stage Data - SASSTO
- Stage 1. 1 x SASSTO. Gross Mass: 97,976 kg (216,000 lb). Empty Mass: 6,668 kg (14,700 lb). Thrust (vac): 1,558.100 kN (350,275 lbf). Isp: 464 sec. Burn time: 300 sec. Isp(sl): 367 sec. Diameter: 6.60 m (21.60 ft). Span: 6.60 m (21.60 ft). Length: 18.80 m (61.60 ft). Propellants: Lox/LH2. No Engines: 1. Engine: Plug-Nozzle SASSTO. Other designations: Saturn Applications Single Stage to Orbit. Status: Study 1967. Comments: Recoverable S-IVB with plug nozzle engine. 36 x plug-nozzle engines (102 atm chamber pressure, 6:1 mixture ratio).
Status: Study 1967.
Gross mass: 97,887 kg (215,803 lb).
Payload: 2,812 kg (6,199 lb).
Height: 21.00 m (68.00 ft).
Diameter: 6.71 m (22.01 ft).
Thrust: 1,232.18 kN (277,005 lbf).
Apogee
No comments:
Post a Comment