From Wikipedia, the free encyclopedia
A Space Shuttle rocketing into space, just after booster separation.
Only five spaceplanes have successfully flown to date, having reentered Earth's atmosphere, returned to Earth, and safely landed — the North American X-15, Space Shuttle, Buran, SpaceShipOne, and Boeing X-37. All five are considered rocket gliders. As of 2015, only these aircraft and rockets have succeeded in reaching space. Two of these five (X-15 and SpaceShipOne) are rocket-powered aircraft, having been carried up to an altitude of several tens of thousands of feet by an atmospheric mother ship before being released, and then flying beyond the boundaries of the earth's atmosphere under their own power. Three (Space Shuttle, Buran, and X-37) are vertical takeoff horizontal landing (VTHL) vehicles relying upon rocket lift for the ascent phase in reaching space and atmospheric lift for reentry, descent and landing. The three VTHL spaceplanes flew much further than the aircraft launched ones, not merely leaving the earth's atmosphere but also entering orbit around it, which requires at least 50 times more energy on the way up and heavy heat shielding for the trip back.[2] Also, of the 5 vehicles, three have been piloted by astronauts, with the Buran and X-37 flying unmanned missions.
Contents
Description
Landing of NASA Space Shuttle Atlantis. The American Space Shuttles were manned orbital spaceplanes.
Aerodynamic lift
Main article: Lift (force)
All aircraft utilize aerodynamic surfaces in order to generate lift. For spaceplanes a variety of wing shapes can be used. Delta wings are common, but straight wings, lifting bodies and even rotorcraft have been proposed. Typically the force of lift generated by these surfaces is many times that of the drag that they induce.[citation needed]Atmospheric reentry
Main article: Atmospheric entry
Because suborbital spaceplanes are designed for trajectories that do not reach orbital speed, they do not need the kinds of thermal protection orbital spacecraft required during the hypersonic phase of atmospheric reentry. The Space Shuttle thermal protection system,
for example, protects the orbiter from surface temperatures that could
otherwise reach as high as 1,650 °C (3,000 °F), well above the melting
point of steel.[3]Aircraft landing
Main article: Landing § Aircraft
A spaceplane operates as an aircraft in Earth's atmosphere. Aircraft may land on firm runways, helicopter landing pads, or even water (amphibious aircraft), snow or ice. To land, the airspeed and the rate of descent
are reduced such that the aircraft descends at a slow enough rate to
allow for a gentle touch down. Landing is accomplished by slowing down
and descending. This speed reduction is accomplished by reducing thrust
and/or inducing a greater amount of drag using flaps, landing gear or speed brakes. Splashdown is an easier technical feat to accomplish, requiring only the deployment of a parachute (or parachutes), rather than successfully aviating the atmosphere.[4]
Project Gemini's original concept design was as a spaceplane, with
paraglider and wheels (or skis) attached. However, this concept was
abandoned in favor of parachute splashdowns, because of expensive
technical failures during testing and development. Whereas Project
Gemini's splashdown parachutes took only 5 months to develop in 1963,
Gemini's spaceplane concept failed to materialize even after nearly 3
years of continued development.Propulsion
Buran orbiter rear showing rocket engine nozzles, for maneuvering in low Earth orbit and thin air
Rocket engines
All spaceplanes to date have used rocket engines with chemical fuels. As the orbital insertion burn has to be done in space, orbital spaceplanes require rocket engines for at least that portion of the flight.Airbreathing engines
Main article: Airbreathing jet engine
A difference between rocket based and air-breathing aerospace plane
launch systems is that aerospace plane designs typically include minimal
oxidizer storage for propulsion. Air-breathing aerospace plane designs include engine inlets so they can use atmospheric oxygen for combustion. Since the mass of the oxidizer is, at takeoff, the single largest mass of most rocket designs (the Space Shuttle's liquid oxygen tank weighs 629,340 kg, more than one of its solid rocket boosters[5]),
this provides a huge potential weight savings benefit. However, air
breathing engines are usually very much heavier than rocket engines and
the empty weight of the oxidiser tank, and since, unlike oxidiser, this
extra weight (which is not expended to add kinetic energy to the vessel,
as is propellant mass) must be carried into space it may offset the
overall system performance.[citation needed]Types of air breathing engines proposed for spaceplanes include scramjet, liquid air cycle engines, precooled jet engines, pulse detonation engine and ramjets. Some engine designs combine several types of engines features into a combined cycle. For instance, the Rocket-based combined cycle (RBCC) engine uses a rocket engine inside a ramscoop so that at low speed, the rockets thrust is boosted by ejector augmented thrust. It then transitions to ramjet propulsion at near-supersonic speeds, then to supersonic combustion or scramjet propulsion, above Mach 6, then back to pure rocket propulsion above Mach 10.[citation needed]
Harsh flight environment
The flight trajectory required of air-breathing aerospace vehicles to reach orbit is to fly what is known as a 'depressed trajectory' which places the aerospace plane in the high-altitude hypersonic flight regime of the atmosphere. This environment induces high dynamic pressure, high temperature, and high heat flow loads particularly upon the leading edge surfaces of the aerospace plane. These loads typically require special advanced materials, active cooling, or both, for the structures to survive the environment.Rocket-powered spaceplanes also face a significant thermal environment if they are burning for orbit, but this is nevertheless far less severe than air-breathing spaceplanes.[citation needed]
Suborbital space planes designed to briefly reach space do not require significant thermal protection, as they experience peak heating for only a short time during re-entry. Intercontinental suborbital trajectories require much higher speeds and thermal protection more similar to orbital spacecraft reentry.[citation needed]
Center of mass issues
A wingless launch vehicle has lower aerodynamic forces affecting the vehicle, and attitude control can be active perhaps with some fins to aid stability. For a winged vehicle the centre of lift moves during the atmospheric flight as well as the centre of mass; and the vehicle spends longer in the atmosphere as well. Historically, the X-33 and HOTOL spaceplanes were rear engined and had relatively heavy engines. This puts a heavy mass at the rear of the aircraft with wings that had to hold up the vehicle. As the wet mass reduces, the centre of mass tends to move rearward behind the centre of lift, which tends to be around the centre of the wings. This can cause severe instability that is usually solved by extra fins which add weight and decrease performance.[citation needed]Flown spaceplanes
World's first spaceplanes: North American X-15, Space Shuttle, Buran, SpaceShipOne, Boeing X-37. The X-15 reached space in 1962/1963 (USAF/FAI Kármán line classifications). SpaceShipOne was piloted by the first commercial astronaut. Both X-15 and SpaceShipOne ascend horizontally from a mother ship. Both Buran and X-37 spaceflights were unmanned. The X-37 launches atop an Atlas V 501 launch vehicle.[6]
Orbital spaceplanes
All three of the orbital spaceplanes successfully flown to date utilize a VTHL (vertical takeoff, horizontal landing) design. They include the piloted United States Space Shuttle and two unmanned spaceplanes: the late-1980s Soviet Buran and the early-2010s Boeing X-37.The early-1980s BOR-4 (subscale test vehicle for the Spiral spaceplane that was subsequently cancelled) was a spacecraft that did successfully reenter the atmosphere and fly like an aircraft. But it was not designed to sustain atmospheric flight. It was designed to stop flying, open a parachute and then splash in the ocean.
These vehicles have used wings to provide aerobraking to return from orbit and to provide lift, allowing them to land on a runway like conventional aircraft. These vehicles are still designed to ascend to orbit vertically under rocket power like conventional expendable launch vehicles. One drawback of spaceplanes is that they have a significantly smaller payload fraction than a ballistic design with the same takeoff weight. This is in part due to the weight of the wings — around 9-12% of the weight of the atmospheric flight weight of the vehicle. This significantly reduces the payload size, but the reusability is intended to offset this disadvantage.
While all spaceplanes have used atmospheric lift for the reentry phase, none to date have succeeded in a design that relies on aerodynamic lift for the ascent phase in reaching space (excluding a mother ship first stage). Efforts such as the Silbervogel and X-30/X-33 have all failed to materialize into a vehicle capable of successfully reaching space. The Pegasus winged booster has had many successful flights to deploy orbital payloads, but since its aerodynamic vehicle component operates only as a booster, and not operate in space as a spacecraft, it is not typically considered to be a spaceplane.[citation needed]
On the other hand, OREX[7] is a test vehicle of HOPE-X and launched into 450 km LEO using H-II in 1994. OREX succeeded to reenter, but it was only hemispherical head of HOPE-X, that is, not plane-shaped.
Suborbital spaceplanes
Main article: Suborbital spaceplane
The X-15's rocket engine used ammonia and liquid oxygen.
SpaceShipOne Space plane
XCOR Aerospace signed a $30 million contract with Yecheon Astro Space Center to build and lease its Lynx Mark II spaceplane, which would be designed to take off from a runway under its own rocket power, and to reach the same altitude and speed range as SpaceShipOne and SpaceShipTwo, due to the fact that Lynx is propelled by higher specific impulse fuels. Lynx is designed to only carry a pilot and one passenger, although tickets are expected to be around half those quoted for Virgin Galactic services.[9]
Hyflex[10][11] was a miniaturized suborbital demonstrator of HOPE-X launched in 1996. Hyflex flew to 110 km altitude and succeeded in atmospheric reentry, subsequently achieving hypersonic flight. Though Hyflex achieved a controlled aircraft descent, it was not designed for a planned aircraft landing, the engineers opting instead for a splashdown without a parachute. The Hyflex that flew failed to recover and sank in the Pacific Ocean.
See also: Rocket-powered aircraft
Other projects
United States Gemini spaceplane concept testing, August 1964.
United States
The U.S. Air Force invested some effort in a paper study of a variety of spaceplane projects under their Aerospaceplane efforts of the late 1950s, but later ended these when they decided to use a modified version of Sänger's design. The result, Boeing X-20 Dyna-Soar, was to have been the first orbital spaceplane, but was canceled in the early 1960s in lieu of NASA's Project Gemini and the U.S. Air Force's Manned Orbiting Laboratory program.In 1961, NASA originally planned to have the Gemini spacecraft land on a firm, solid ground runway[12] with a Rogallo wing airfoil,[13] rather than as a splashdown with parachute.[13] The test vehicle became known as the Paraglider Research Vehicle. Development work on both Gemini's splashdown parachute and spaceplane paraglider began in 1963.[14] By December 1963, the parachute was already to undergo full-scale deployment testing.[14] On the other hand, by December 1963 the paraglider spaceplane concept was running into technical difficulties[12] and subsequently became replaced by the parachute splashdown concept.[14] Though attempts to revive Gemini's paraglider spaceplane concept persisted within NASA and North American Aviation as late as 1964,[15] NASA Headquarters Gemini Chief William Schneider discontinued development as technical hurdles became too expensive.[15]
United States STS Space shuttle concepts circa 1970s
The Lockheed Martin X-33 was a prototype made as part of an attempt by NASA to build a SSTO hydrogen-fuelled spaceplane VentureStar that failed when the hydrogen tank design proved to be unconstructable in the planned way. The March 5, 2006 edition of Aviation Week & Space Technology published a story purporting to be "outing" a highly classified U.S. military two-stage-to-orbit spaceplane system with the code name Blackstar, SR-3/XOV among other nicknames.[citation needed]
Boeing X-37B being prepared for launch in 2010 on an expendable orbital rocket
Boeing has proposed that a larger variant of the X-37B, the X-37C could be built to carry up to six passengers up to LEO. The spaceplane would also be usable for carrying cargo, with both upmass and downmass (return to Earth) cargo capacity. The ideal size for the proposed derivative "is approximately 165 to 180 percent of the current X-37B."[18]
In December 2010, Orbital Sciences made a commercial proposal to NASA to develop the Prometheus, a lifting-body spaceplane vehicle about one-quarter the size of the Space Shuttle, in response to NASA's Commercial Crew Development (CCDev) phase 2 solicitation. The vehicle would be launched on a human-rated (upgraded) Atlas V rocket but would land on a runway.[19] For the same solicitation, Sierra Nevada Corporation proposed phase 2 extensions of its Dream Chaser spaceplane technology, partially developed under the first phase of NASA's CCDev program.[20] Both the Orbital Sciences proposal and the Dream Chaser are lifting body designs.[21] Sierra Nevada will utilize Virgin Galactic to market Dream Chaser commercial services and may use "Virgin’s WhiteKnightTwo carrier aircraft as a platform for drop trials of the Dream Chaser atmospheric test vehicle"[20][22] NASA expects to make approximately $200 million of phase 2 awards by March 2011, for technology development projects that could last up to 14 months.[23]
National Aerospace Plane
Main article: Rockwell X-30
NASP taking off
There were six identifiable technologies which were considered critical to the success of the NASP project. Three of these "enabling" technologies were related to the propulsion system, which would consist of a hydrogen-fueled scramjet.[24] The NASP program became the Hypersonic Systems Technology Program (HySTP) in late 1994.
HySTP was designed to transfer the accomplishments made in hypersonic technologies by the National Aero-Space Plane (NASP) program into a technology development program. On January 27, 1995 the Air Force terminated participation in (HySTP).[24]
Soviet Union and Russia
Buran orbiter being transported via An-225
Cosmoplane
In recent times, an orbital spaceplane, called cosmoplane (Russian: космоплан) capable of transporting passengers has been proposed by Russia's Institute of Applied Mechanics. According to researchers, it could take about 20 minutes to fly from Moscow to Paris, using hydrogen and oxygen-fueled engines.[26][27]United Kingdom
The lead engineer from the HOTOL project has since set up a private company dedicated to creating a similar plane called Skylon with a different combined cycle rocket/turbine precooled jet engine called SABRE. This vehicle is intended to be capable of a single stage to orbit launch carrying a 15,000 kg payload into Low Earth Orbit. If successful it would be far in advance of anything currently in operation.[30]
The British company Bristol Spaceplanes has undertaken design and prototyping of three potential spaceplanes since its founding by David Ashford in 1991. The European Space Agency has endorsed these designs on several occasions.[31]
France and the European Space Agency
France worked on the Hermes manned spaceplane launched by Ariane rocket in the late 20th century, and proposed in January 1985 to go through with Hermes development under the auspices of the ESA.[32] Hopper was one of several proposals for a European reusable launch vehicle (RLV) planned to cheaply ferry satellites into orbit by 2015.[33] One of those was 'Phoenix', a German project which is a one-seventh scale model of the Hopper concept vehicle.[34] The suborbital Hopper was a FESTIP (Future European Space Transportation Investigations Programme) system study design[35] A test project, the Intermediate eXperimental Vehicle (IXV), has demonstrated lifting reentry technologies and will be extended under the PRIDE programme.[36]Japan
HOPE was a Japanese experimental spaceplane project designed by a partnership between NASDA and NAL (both now part of JAXA), started in the 1980s. It was positioned for most of its lifetime as one of the main Japanese contributions to the International Space Station, the other being the Japanese Experiment Module. The project was eventually cancelled in 2003, by which point test flights of a sub-scale testbed had flown successfully.Germany
After the German Sänger-Bredt RaBo and Silbervogel of the 1930s and 1940s, Eugen Sänger worked for time on various space plane projects, coming up with several designs for Messerschmitt-Bölkow-Blohm such as the MBB Raumtransporter-8.[37] In the 1980s, West Germany funded design work on the MBB Sänger II with the Hypersonic Technology Program. Development continued on MBB/Deutsche Aerospace Sänger II/HORUS until the late 1980s when it was canceled. Germany went on to participate in the Ariane rocket, Columbus space station and Hermes spaceplane of ESA, Spacelab of ESA-NASA and Deutschland missions (non-U.S. funded Space Shuttle flights with Spacelab). The Sänger II had predicted cost savings of up to 30 percent over expendable rockets.[38][39] The Daimler-Chrysler Aerospace RLV was a much later small reusable spaceplane prototype for ESA FLPP/FLTP program.India
AVATAR (Sanskrit: अवतार) (from "Aerobic Vehicle for Hypersonic Aerospace TrAnspoRtation") is an early-2000s concept of a manned single-stage reusable spaceplane capable of horizontal takeoff and landing, by India's Defence Research and Development Organisation, the Indian Space Research Organisation (ISRO) and other research institutions, intended for both military and civilian satellite launches. The ISRO plans to test the concept with a scaled-down suborbital Reusable Launch Vehicle-Technology Demonstrator (RLV-TD) spaceplane in 2015,[40] and aims to fly the full prototype by 2025.[41]China
Main article: Shenlong (spacecraft)
Shenlong (Chinese: 神龙; pinyin: shén lóng; literally: "divine dragon") is a proposed Chinese robotic space plane that is similar to the American Boeing X-37.[42] Only a few images have been released since late 2007.[43][44][45]Boeing X-37
From Wikipedia, the free encyclopedia
X-37 | |
---|---|
![]() |
|
The OTV-1 X-37B in April 2010, inside its payload fairing prior to launch | |
Role | Unmanned spaceplane |
National origin | United States |
Manufacturer | Boeing Defense, Space & Security |
First flight | 7 April 2006 (first drop test) |
Introduction | 22 April 2010 (first spaceflight) |
Status | 3 spaceflights completed[1][2][3] 1 spaceflight in progress[4] |
Primary user | X-37A: NASA/DARPA X-37B: United States Air Force |
Number built | X-37A: 1 X-37B: 2 |
Developed from | Boeing X-40 |
The Boeing X-37, also known as the Orbital Test Vehicle (OTV), is a reusable unmanned spacecraft. It is boosted into space by a launch vehicle, then re-enters Earth's atmosphere and lands as a spaceplane. The X-37 is operated by the United States Air Force for orbital spaceflight missions intended to demonstrate reusable space technologies.[5] It is a 120%-scaled derivative of the earlier Boeing X-40.
The X-37 began as a NASA project in 1999, before being transferred to the U.S. Department of Defense in 2004. It conducted its first flight as a drop test on 7 April 2006, at Edwards Air Force Base, California. The spaceplane's first orbital mission, USA-212, was launched on 22 April 2010 using an Atlas V rocket. Its successful return to Earth on 3 December 2010 was the first test of the vehicle's heat shield and hypersonic aerodynamic handling. A second X-37 was launched on 5 March 2011, with the mission designation USA-226; it returned to Earth on 16 June 2012. A third X-37 mission, USA-240, launched on 11 December 2012 and landed at Vandenberg AFB on 17 October 2014. The fourth X-37 mission, USA-261, launched on 20 May 2015 and is in progress.
Contents
Development
Origins
In 1999, NASA selected Boeing Integrated Defense Systems to design and develop an orbital vehicle, built by the California branch of Boeing's Phantom Works. Over a four-year period, a total of $192 million was contributed to the project, with NASA contributing $109 million, the U.S. Air Force $16 million, and Boeing $67 million. In late 2002, a new $301-million contract was awarded to Boeing as part of NASA's Space Launch Initiative framework.[6]
1999 artist's rendering of the X-37 spacecraft
The X-37 was transferred from NASA to the Defense Advanced Research Projects Agency (DARPA) on 13 September 2004.[11] Thereafter, the program became a classified project. DARPA promoted the X-37 as part of the independent space policy that the United States Department of Defense has pursued since the 1986 Challenger disaster.
Glide testing
The vehicle that was used as an atmospheric drop test glider had no propulsion system. Instead of an operational vehicle's payload bay doors, it had an enclosed and reinforced upper fuselage structure to allow it to be mated with a mothership. In September 2004, DARPA announced that for its initial atmospheric drop tests the X-37 would be launched from the Scaled Composites White Knight, a high-altitude research aircraft.[12]
The Scaled Composites White Knight was used to launch the X-37A on glide tests.
On 24 March 2006, the X-37 flew again, but a datalink failure prevented a free flight, and the vehicle returned to the ground still attached to its White Knight carrier aircraft. On 7 April 2006, the X-37 made its first free glide flight. During landing, the vehicle overran the runway and sustained minor damage.[16] Following the vehicle's extended downtime for repairs, the program moved from Mojave to Air Force Plant 42 (KPMD) in Palmdale, California for the remainder of the flight test program. White Knight continued to be based at Mojave, though it was ferried to Plant 42 when test flights were scheduled. Five additional flights were performed,[N 1] two of which resulted in X-37 releases with successful landings. These two free flights occurred on 18 August 2006 and 26 September 2006.[17]
X-37B Orbital Test Vehicle
On 17 November 2006, the U.S. Air Force announced that it would develop its own variant from NASA's X-37A. The Air Force version was designated the X-37B Orbital Test Vehicle (OTV). The OTV program was built on earlier industry and government efforts by DARPA, NASA and the Air Force, and was led by the U.S. Air Force Rapid Capabilities Office, in partnership with NASA and the Air Force Research Laboratory. Boeing was the prime contractor for the OTV program.[8][18][19] The X-37B was designed to remain in orbit for up to 270 days at a time.[20] The Secretary of the Air Force stated that the OTV program would focus on "risk reduction, experimentation, and operational concept development for reusable space vehicle technologies, in support of long-term developmental space objectives."[18]The X-37B was originally scheduled for launch in the payload bay of the Space Shuttle, but following the 2003 Columbia disaster, it was transferred to a Delta II 7920. The X-37B was subsequently transferred to a shrouded configuration on the Atlas V rocket, following concerns over the unshrouded spacecraft's aerodynamic properties during launch.[21] Following their missions, X-37B spacecraft land on a runway at Vandenberg Air Force Base, California, with Edwards Air Force Base as an alternate site.[22] In 2010, manufacturing work began on the second X-37B, OTV-2,[23] which conducted its maiden launch in March 2011.[24]
On 8 October 2014, NASA confirmed that X-37B vehicles would be housed at Kennedy Space Center in Orbiter Processing Facilities (OPF) 1 and 2, hangars previously occupied by the Space Shuttle. Boeing had said the space planes would use OPF-1 in January 2014, and the Air Force had previously said it was considering consolidating X-37B operations, housed at Vandenberg Air Force Base in California, nearer to their launch site at Cape Canaveral. NASA also stated that the program had completed tests to determine whether the X-37B, one-fourth the size of the Space Shuttle, could land on the former Shuttle runways.[25] NASA furthermore stated that renovations of the two hangars would be completed by the end of 2014; the main doors of OPF-1 were marked with the message "Home of the X-37B" by this point.[25]
Most of the activities of the X-37B project are secret. The official U.S. Air Force statement is that the project is "an experimental test program to demonstrate technologies for a reliable, reusable, unmanned space test platform for the U.S. Air Force."[5] The primary objectives of the X-37B are twofold: reusable spacecraft technology, and operating experiments which can be returned to Earth.[5] The Air Force states that this includes testing avionics, flight systems, guidance and navigation, thermal protection, insulation, propulsion, and re-entry systems.[26]
Speculation regarding purpose
In 2010, Tom Burghardt wrote for Space Daily that the X-37B could be used as a spy satellite or to deliver weapons from space.[27] The Pentagon subsequently denied claims that the X-37B's test missions supported the development of space-based weapons.[27] In January 2012, allegations were made that the X-37B was being used to spy on China's Tiangong-1 space station module.[28]Former U.S. Air Force orbital analyst Brian Weeden later refuted this claim, emphasizing that the different orbits of the two spacecraft precluded any practical surveillance fly-bys.[29] In October 2014, The Guardian reported the claims of security experts that the X-37B was being used "to test reconnaissance and spy sensors, particularly how they hold up against radiation and other hazards of orbit."[30]
Design
At the time of its maiden launch, the X-37 (far right) was the smallest and lightest orbital spaceplane yet flown. Both the North American X-15 and SpaceShipOne were suborbital. Of the spaceplanes shown, only the X-37 and Buran conducted unmanned spaceflights.
The technologies demonstrated in the X-37 include an improved thermal protection system, enhanced avionics, an autonomous guidance system and an advanced airframe.[10] The spaceplane's thermal protection system is built upon previous generations of atmospheric reentry spacecraft,[34] incorporating silica ceramic tiles.[35] The X-37's avionics suite was used by Boeing to develop its CST-100 manned spacecraft.[36] According to NASA, the development of the X-37 will "aid in the design and development of NASA's Orbital Space Plane, designed to provide a crew rescue and crew transport capability to and from the International Space Station".[37]
The X-37 is independently powered by one Aerojet AR2-3 engine using storable propellants, providing thrust of 6,600 pounds-force (29.341 kN).[38] The human-rated AR2-3 engine had been used on the dual-power NF-104A astronaut training vehicle, and was given a new flight certification for use on the X-37 with hydrogen peroxide/JP-8 propellants.[39]
The X-37 lands automatically upon returning from orbit, and is the second reusable spacecraft to have such a capability, after the Soviet Buran shuttle.[40] The X-37 is the smallest and lightest orbital spaceplane flown to date; with a launch mass of around 11,000 pounds (5,000 kg), it is approximately a quarter the size of the Space Shuttle orbiter.[41] In 2013, Guinness World Records recognised the X-37 as the world's smallest orbital spaceplane.[42]
The Space Foundation awarded the X-37 team on 13 April 2015 with the 2015 Space Achievement Award "for significantly advancing the state of the art for reusable spacecraft and on-orbit operations, with the design, development, test and orbital operation of the X-37B space flight vehicle over three missions totaling 1,367 days in space."[43]
Operational history
As of 17 October 2014, the two operational X-37Bs have conducted three orbital missions, spending a combined total 1,367 days in space.[44]OTV-1
Main article: USA-212
OTV-1 sits on the runway after landing at Vandenberg AFB at the close of its USA-212 mission on 3 December 2010.
The U.S. Air Force announced on 30 November 2010 that OTV-1 would return for a landing during the 3–6 December timeframe.[48][49] As scheduled, OTV-1 de-orbited, reentered Earth's atmosphere, and landed successfully at Vandenberg AFB on 3 December 2010, at 09:16 UTC,[50][51][52] conducting America's first autonomous orbital landing onto a runway; the first spacecraft to perform such a feat was the Soviet Buran shuttle in 1988. In all, OTV-1 spent 224 days in space.[53] OTV-1 suffered a tire blowout during landing and sustained minor damage to its underside.[23]
OTV-2
Main article: USA-226
OTV-2, the second X-37B, launched on its inaugural mission, designated USA-226,[54] aboard an Atlas V rocket from Cape Canaveral on 5 March 2011.[55] The mission was classified and described by the U.S. military as an effort to test new space technologies.[56]
On 29 November 2011, the U.S. Air Force announced that it would extend
the mission of USA-226 beyond the 270-day baseline design duration.[53] In April 2012, General William L. Shelton of the Air Force Space Command declared the ongoing mission a "spectacular success".[57]On 30 May 2012, the Air Force stated that OTV-2 would complete its mission and land at Vandenberg AFB in June 2012.[58][59] The spacecraft landed autonomously on 16 June 2012, having spent 469 days in space.[1][60]
OTV-3
Main article: USA-240
OTV-3, the second mission for the first X-37B and the third X-37B
mission overall, was originally scheduled to launch on 25 October 2012,[61] but was postponed because of an engine issue with the Atlas V launch vehicle.[62] The X-37B was successfully launched from Cape Canaveral on 11 December 2012.[41][63][64] The launch was designated USA-240.[65][66]
The OTV-3 mission ended with a landing at Vandenberg AFB on 17 October
2014 at 16:24 UTC, after a total time in orbit of just under 675 days.[3][67]OTV-4
The Air Force launched a fourth X-37B mission, designated OTV-4 and codenamed AFSPC-5, aboard an Atlas V rocket from Cape Canaveral Air Force Station on 20 May 2015.[44][68] The launch was designated USA-261 and is the second flight of the second X-37B vehicle.[21] The mission will test a Hall effect thruster in support of the Advanced Extremely High Frequency communications satellite program,[68] and conduct a NASA investigation for testing various materials in space.[4][21][43] The mission is expected to last at least 200 days,[21] and as of 8 December 2015 the vehicle remains in orbit.[69]Variants
X-37A
The X-37A was the initial NASA version of the spacecraft; the X-37A Approach and Landing Test Vehicle (ALTV) was used in drop glide tests in 2005 and 2006.[14][70]X-37B
The X-37B is a modified version of the NASA X-37A, intended for the U.S. Air Force.[5] It conducted multiple orbital test missions.[63]X-37C
In 2011, Boeing announced plans for a scaled-up variant of the X-37B, referring to it as the X-37C. The X-37C spacecraft would be between 165% and 180% of the size of the X-37B, allowing it to transport up to six astronauts inside a pressurized compartment housed in the cargo bay. Its proposed launch vehicle is the Atlas V Evolved Expendable Launch Vehicle.[71] In this role, the X-37C could potentially compete with Boeing's CST-100 commercial space capsule.[72]Specifications
X-37B
General characteristics- Crew: none
- Length: 29 ft 3 in (8.92 m)
- Wingspan: 14 ft 11 in (4.55 m)
- Height: 9 ft 6 in (2.90 m)
- Max takeoff weight: 11,000 lb (4,990 kg)
- Electrical power: Gallium arsenide solar cells with lithium-ion batteries[5]
- Payload bay: 7 × 4 ft (2.1 × 1.2 m)[73]
- Powerplant: 1 × Aerojet AR2-3 rocket engine, 6,596 lbf (29.341 kN) thrust using hydrogen peroxide and JP-8 fuel[38]
- Orbital speed: 28,044 km/h (17,426 mph)[75]
- Orbit: Low Earth orbit
- Orbital time: 270 days (design)[76][N 2]
Skylon (spacecraft)
From Wikipedia, the free encyclopedia
For other uses of Skylon, see Skylon (disambiguation).
Skylon | |
---|---|
![]() |
|
The Skylon vehicle is intended to be an aircraft designed to reach orbit. | |
Role | Re-usable spaceplane |
National origin | United Kingdom |
Designer | Reaction Engines Limited |
First flight | 2025 - Proposed test flight[1] |
Status | Research and development |
Program cost | Projected to be £7.1 billion[2] (~$12 billion est. 2004)[3] |
Unit cost |
£190 million (projected)[2]
|
Developed from | HOTOL (Horizontal Take-Off and Landing) project |
Skylon is a design for a single-stage-to-orbit spaceplane by the British company Reaction Engines Limited (REL), using SABRE, a combined-cycle, air-breathing rocket propulsion system, potentially reusable for 200 flights. In paper studies, the cost per kilogram of payload carried to low Earth orbit in this way is hoped to be reduced from the current £1,108/kg (as of December 2015),[4] including research and development, to around £650/kg, with costs expected to fall much more over time after initial expenditures have amortised.[3] In 2004, the developer estimated the total lifetime cost of the programme to be about $12 billion.[3]
The vehicle design is for a hydrogen-fuelled aircraft that would take off from a purpose-built runway, and accelerate to Mach 5.4 at 26 kilometres (16 mi) altitude using the atmosphere's oxygen before switching the engines to use the internal liquid oxygen (LOX) supply to take it into orbit.[5]:5 Once in orbit it would release its payload of up to 15 tonnes. The vehicle will be unpiloted, but also be certified to carry passengers. All payloads could be carried in a standardised container compartment. The relatively light vehicle would then re-enter the atmosphere and land on a runway, being protected from the conditions of re-entry by a ceramic composite skin. When on the ground it would undergo inspection and necessary maintenance. If the design goal is achieved, it should be ready to fly again within two days.
As of 2012, only a small portion of the funding required to develop and build Skylon had been secured. The research and development work on the SABRE engine design is proceeding under a small European Space Agency (ESA) grant. In January 2011, REL submitted a proposal to the British government to request additional funding for the project and in April REL announced that they had secured $350 million of further funding contingent on a test of the engine's precooler technology being successful. Testing of the key technologies was successfully completed in November 2012, allowing Skylon's design to advance to its final phase.[6][7] On 16 July 2013 the British government pledged £60M to the project: this investment will provide support at a "crucial stage" to allow a full-scale prototype of the SABRE engine to be built.[8]
If all goes to plan, the first ground-based engine tests could happen in 2019, and Skylon could be performing unmanned test flights by 2025.[1] It could carry 15 tonnes of cargo to a 300 km equatorial orbit on each trip, and up to 11 tonnes to the International Space Station, almost 45% more than the capacity of the European Space Agency's ATV vehicle.[9]
Contents
Research and development programme
Background and early work
Skylon is based on a previous project of Alan Bond, known as HOTOL.[10] The development of HOTOL began in 1982, at a time when space technology was moving towards reusable launch systems such as the Space Shuttle. In conjunction with British Aerospace and Rolls-Royce, a promising design emerged to which the British government contributed £2 million. However, in 1988, the government withdrew further funding, and development was terminated. Following this setback, Bond decided to set up his own company, Reaction Engines Limited, with the hope of continuing development with private funding.
The Skylon was developed from the British HOTOL project.
There are several differences compared with HOTOL. Whereas HOTOL would have launched from a rocket sled, to save weight, Skylon uses a conventional retractable undercarriage. Skylon's revised engine design, the SABRE engine, is expected to offer higher performance.[5]:4 HOTOL's rear mounted engine gave the vehicle intrinsically poor in-flight stability. Skylon solves this by placing engines at the end of its wings, but further forward and much closer to the vehicle's centre of mass longitudinally. Early attempts to fix this problem had ended up sacrificing much of HOTOL's payload potential, and contributed to the failure of the project.[5]:11
Project brief
A computer-generated image of the Skylon spaceplane climbing to orbit.
In service, Skylon could potentially lower satellite launch costs from the current £15,000/kg to £650/kg, according to evidence submitted to the UK parliament by Reaction Engines Ltd.[15] Funding for the project from the British government has often been difficult to obtain.[16] Speaking on the topic of Skylon in 2011, David Willetts, the UK Minister of State for Universities and Science, stated:
The European Space Agency is funding proof of concept work for Skylon from UK contributions. This work is focusing on demonstrating the viability of the advanced British engine technology that would underpin the project. Initial work will be completed in mid 2011 and if the trial is successful, we will work with industry to consider next steps.[15]
Funding and engine development
An unsuccessful request for funding from the British government was issued in 2000. This involved a proposal offering a potentially large return on investment.[17] Subsequent discussions with the British National Space Centre (which later became the UK Space Agency) led to a major funding agreement in February 2009 between the British National Space Centre, European Space Agency (ESA) and REL for €1 million ($1.28 million) to produce a demonstration engine for Skylon by 2011.[18][19][20]The Technology Demonstration Programme will last approximately 2.5 years and will benefit from another €1 million from ESA.[21] This programme will take Reaction Engines Ltd from a Technology Readiness Level (TRL) of 2/3 up to 4/5.[22] The former UK Minister for Science and Innovation in 2009, Lord Drayson, commented on Skylon in a speech: "This is an example of a British company developing world-beating technology with exciting consequences for the future of space."[15]
As of 2012, the funding required to develop and build the entire craft has not yet been secured, and so current research and development work is focused on the engines, under an ESA grant of €1 million.[23] In January 2011, REL submitted a proposal to the British Government requesting additional funding for the Skylon project.[15] On 13 April 2011, REL announced that the Skylon design had passed several rigorous independent reviews. On 24 May 2011, ESA publicly declared the design to be feasible, having found "no impediments or critical items" in the proposal.[24]
The precooler rig that tested the heat exchange system of the SABRE engine.
On 9 May 2011, REL stated that a preproduction prototype of the Skylon could be flying by 2016, and the proposed route would be a suborbital flight between the Guiana Space Centre near Kourou in French Guiana and the North European Aerospace Test Range, located in northern Sweden.[28] Pre-orders are expected in the 2011–2013 time frame coinciding with the formation of the manufacturing consortium.[15] On 8 December 2011, Alan Bond, speaking at the 7th Appleton Space Conference, stated that Skylon would enter into service by 2021-2022 instead of 2020 as previously envisaged.[29]
In April 2012, REL announced that the first phase of the precooler test programme had been successfully completed. On 10 July 2012, REL announced that the second of three series of tests has been completed successfully.[30] The test facilities underwent upgrades to allow the third and final phase of testing to proceed.[31] On 13 July 2012, ESA Director-General Jean-Jacques Dordain told Space News that ESA would hold talks with REL to develop a further "technical understanding".[32]
Following a successful propulsion system test that was audited by ESA's propulsion division in mid-2012, the company announced that it would begin a three-and-a-half-year project to develop and build a test rig of the Sabre engine to prove the engine's performance across its air-breathing and rocket modes.[6] In November 2012, it was announced that a key test of the engine precooler had been successfully completed, and that ESA had verified the precooler's design. The project's development is now allowed to advance to its next phase, which involves the construction and testing of a full-scale prototype engine.[6][33] In June 2013, George Osborne, The Chancellor of the Exchequer stated on his Twitter account that the British government would be giving £60 million towards the further development of the SABRE engine. Osborne's tweet stated: "Just seen SABRE -a rocket engine that cools air from 1000 degrees to -150 in fraction of a second. We're backing the future with £60m funding".[34] This grant was later reduced to £50 million and was approved by the European Commission in August 2015.[35]
In October 2015, BAE Systems entered into an agreement with Reaction Engines where it would invest £20.6 million in Reaction Engines to acquire 20% of its share capital and help develop the SABRE engine.[36][37]
Technology and design
Overview
See also: Single-stage-to-orbit
The Skylon spaceplane is designed as a two-engine, "tailless" aircraft, which is fitted with a steerable canard.
The design of the Skylon C2 features a large cylindrical payload bay, 13 m (42 ft 8 in) long and 4.8 m (15 ft 9 in) in diameter.[5]:12 It is designed to be comparable with current payload dimensions, and able to support the containerisation of payloads that Reaction Engines hopes for in the future.[5]:12 To an equatorial orbit, Skylon could deliver 15 t (33,000 lb) to a 300 km (190 mi) altitude or 11 t (24,000 lb) to an 800 km (500 mi) altitude.[5]:7 Using interchangeable payload containers, Skylon could be fitted to carry satellites or fluid cargo into orbit, or, in a specialised habitation module, up to 30 astronauts in one launch.[39][40]
Because the engine uses the atmosphere as reaction mass at low altitude, it will have a high specific impulse (around 2,800 seconds), and burn about one fifth of the propellant that would have been required by a conventional rocket.[41] Therefore, it would be able to take off with much less total propellant than conventional systems.[41] This, in turn, means that it does not need as much lift or thrust, which permits smaller engines, and allows conventional wings to be used.[41] While in the atmosphere, using wings to counteract gravity drag is more fuel-efficient than simply expelling propellant (as in a rocket), again reducing the total amount of propellant needed.[41]
The payload fraction would be significantly greater than normal rockets and the vehicle should be fully reusable (200 times or more).[42]
SABRE engines
Main article: SABRE (rocket engine)
One of the significant features of the Skylon design is the engine, called SABRE.[5]:4[41] The engines are designed to operate much like a conventional jet engine[citation needed] to around Mach 5.5 (1,700 m/s),[41] 26 kilometres (16 mi) altitude, beyond which the air inlet closes and the engine operates as a highly efficient rocket to orbital speed.[41] The proposed SABRE engine is not a scramjet, but a jet engine running combined cycles of a precooled jet engine, rocket engine and ramjet.[3]
Originally the key technology for this type of precooled jet engine did
not exist, as it required a heat exchanger that was ten times lighter
than the state of the art.[11] Research conducted since then has achieved the necessary performance.[5]:4[43]Operating an air-breathing jet engine at velocities of up to Mach 5.5 poses numerous engineering problems.[41] Several previous engines proposed by other designers worked well as jet engines but performed poorly as rockets.[41] This engine design aims to be a good jet engine within the atmosphere, as well as being an excellent rocket engine outside.[41] The problem with operating at Mach 5.5 has been that the air coming into the engine rapidly heats up as it is compressed into the engine; due to certain thermodynamic effects, this greatly reduces the thrust that can be produced by burning fuel.[41] Attempts to avoid these issues typically make the engine much heavier (scramjets/ramjets) or greatly reduce the thrust (conventional turbojets/ramjets).[41] In either case the end result is an engine that has a poor thrust to weight ratio at high speeds, resulting in an engine that is too heavy to assist much in reaching orbit.[41]
The SABRE engine design aims to avoid this by using some of the liquid hydrogen fuel to cool helium in a closed-cycle precooler, which quickly reduces the temperature of the air at the inlet.[41] The air is then used for combustion much like in a conventional jet,[41] and once the helium has left the pre-cooler it is further heated by the products of the pre-burner, giving it enough energy to drive the turbine and the liquid hydrogen pump.[41] Because the air is cooled at all speeds, the jet can be built of light alloys and the weight is roughly halved.[41] Additionally, more fuel can be burnt at high speed.[41] Beyond Mach 5.5, the air would become unusably hot despite the cooling, so the air inlet closes and the engine relies solely on on-board liquid oxygen and hydrogen fuel as in a normal rocket.[41]
Fuselage and structure
The fuselage of Skylon is expected to be a carbon-fiber-reinforced polymer space frame; a light and strong structure that supports the weight of the aluminium fuel tanks and to which the ceramic skin is attached.[5]:11 Multiple layers of reflective foil thermal insulation fill the spaces of the frame.[5]:15The currently proposed Skylon model C2 will be a large vehicle, with a length of 82 metres (269 ft) and a diameter of 6.3 metres (21 ft).[44] Because it will use a low-density fuel, liquid hydrogen, a great volume is needed to contain enough energy to reach orbit. The propellant is intended to be kept at low pressure to minimise stress; a vehicle that is both large and light has an advantage during atmospheric reentry compared to other vehicles due to a low ballistic coefficient.[5]:7 Because of the low ballistic coefficient, Skylon would be slowed at higher altitudes where the air is thinner. As a result, the skin of the vehicle would reach only 1,100 K (830 °C).[45] In contrast, the smaller Space Shuttle was heated to 2,000 K on its leading edge, and so employed an extremely heat-resistant but fragile silica thermal protection system. The Skylon design does not require such a system, instead opting for using a far thinner yet durable reinforced ceramic skin.[3] However, due to turbulent flow around the wings during re-entry, some parts of Skylon would need to be actively cooled.[5]:15
Wheels and runway
At a gross takeoff weight of 275 tonnes, of which 220 tonnes is propellant, the vehicle is capable of placing 12 tonnes into an equatorial low Earth orbit.[46] A reinforced runway will be needed to tolerate the high equivalent single wheel load.[47] It will possess a retractable undercarriage with high pressure tyres and water-cooled brakes.[5]:21 If problems were to occur just before a take-off the brakes would be applied to stop the vehicle, the water boiling away to dissipate the heat.[5]:21 Upon a successful take-off, the water would be jettisoned, thus reducing the weight of the undercarriage, in the C1 design 1200 kg of water allows the weight of the brakes alone to be reduced from over 3000 kg to around 415 kg.[46] During landing, the empty vehicle would be far lighter, and hence the water would not be needed.[5]:21Specifications (Skylon D1)
Data from the Skylon User Manual[48]
General characteristics
- Crew: None, remote controlled from ground
- The proposed Skylon Personnel/Logistics Module (SPLM) has provision for a Captain.[48]:43
- Capacity: 0
- Payload: 15,000 kg nominal (33,000 lb nominal)
- Length: 83.133 m[48]:4 (272.75 ft)
- Wingspan: 26.818 m [48]:4 (87.99 ft)
- Height: approx 13.5 m [48]:4 (44 ft)
- Empty weight: 53,400 kg[48]:6 (117,000 lb)
- Loaded weight: 325,000 kg[48]:6 (717,000 lb)
- Powerplant: 2 × SABRE 4 synergistic combined cycle rocket engine, 2,000 kN[48]:6 (450,000 lbf) each
- Fuselage diameter: 6.3 m (20.67 ft)
- Maximum speed: Orbital (air-breathing Mach 5.14, rocket Mach 27.8)[48]:6
- Service ceiling: 28,500 m air-breathing, 90 km SABRE ascent, 600 km exoatmospheric (93,500 ft air breathing, 56 mi rocket ascent, 373 mi exoatmospheric)
- Specific impulse: 4,100 seconds (40,000 N-s/kg)-9,200 seconds (90,000 N-s/kg) air-breathing,[48]:6 460 seconds (4,500 N-s/kg) rocket,[48]:6 465.2 seconds (4,562 N-s/kg) orbital[48]:5
- SABRE engine thrust/weight ratio: up to 14 atmospheric[citation needed]
See also
- Reaction Engines A2, an REL design for an antipodal airliner using similar engine technology
- Reusable launch system
Reusable launch system
From Wikipedia, the free encyclopedia
"RLV" redirects here. For the World War II German Reichsluftverteidigung (RLV), see Defence of the Reich. For the college, see RLV College of Music and Fine Arts.
A reusable launch system (RLS, or reusable launch vehicle, RLV) is a launch system which is capable of launching a payload into space more than once. This contrasts with expendable launch systems, where each launch vehicle is launched once and then discarded.No completely reusable orbital launch system is currently in use.[citation needed] The closest example was the partially reusable Space Shuttle. The orbiter, which included the Space Shuttle main engines, and the two solid rocket boosters, were reused after several months of refitting work for each launch. The external tank and launch vehicle load frame were discarded after each flight.[1][2] However, several at least partially reusable systems are currently under development, such as the Falcon 9.
Orbital RLVs are thought to provide the possibility of low cost and highly reliable access to space. However, reusability implies weight penalties such as non-ablative reentry shielding and possibly a stronger structure to survive multiple uses, and given the lack of experience with these vehicles, the actual costs and reliability are yet to be seen.
Contents
- 1 History
- 2 Reusability concepts
- 2.1 Single stage
- 2.2 Two or more stages to orbit
- 2.3 Biamese & Triamese (Crossfeed)
- 2.4 Horizontal landing
- 2.5 Vertical landing
- 2.6 Horizontal takeoff
- 2.7 Vertical takeoff
- 2.8 Airbreathing
- 2.9 Propellant
- 2.10 Launch assistance
- 2.11 Reentry heat shields
- 2.12 Weight penalty
- 2.13 R&D
- 2.14 Maintenance
- 2.15 Manpower and logistics
- 3 Orbital reusable launchers
- 4 Suborbital reusable launchers
- 5 Regulations
- 6 See also
- 7 References
- 8 Bibliography
- 9 External links
History
ROMBUS
The realities of early engine technology with low specific impulse or insufficient thrust-to-weight ratio to escape Earth's gravity well, compounded by construction materials without adequate performance (strength, stiffness, heat resistance) and low weight, seemingly rendered that original single-stage reusable vehicle vision impossible.
However, advances in materials and engine technology have rendered this concept potentially feasible.
Before VTVL SSTO designs came the partially reusable multi-stage NEXUS launcher by Krafft Arnold Ehricke. The pioneer in the field of VTVL SSTO, Philip Bono, worked at Douglas. Bono proposed several launch vehicles including: ROOST, ROMBUS, Ithacus, Pegasus and SASSTO. Most of his vehicles combined similar innovations to achieve SSTO capability. Bono proposed:
- Plug nozzle engines to retain high specific impulse at all altitudes.
- Base first reentry which allowed the reuse of the engine as a heat shield, lowering required heat shield mass.
- Use of spherical tanks and stubby shape to reduce vehicle structural mass further.
- Use of drop tanks to increase range.
- Use of in-orbit refueling to increase range.
In Europe, Dietrich Koelle, inspired by Bono's SASSTO design, proposed his own VTVL vehicle named BETA.
Before HTHL SSTO designs came Eugen Sänger and his Silbervogel ("Silverbird") suborbital skip bomber. HTHL vehicles which can reach orbital velocity are harder to design than VTVL due to their higher vehicle structural weight. This led to several multi-stage prototypes such as a suborbital X-15. Aerospaceplane being one of the first HTHL SSTO concepts. Proposals have been made to make such a vehicle more viable including:
- Rail boost (e.g. 270 m/s at 3000 m on a mountain allowing 35% less SSTO takeoff mass for a given payload in one NASA study)[3]
- Use of lifting body designs to reduce vehicle structural mass.
- Use of in-flight refueling.
The late 1960s saw the start of the Space Shuttle design process. From an initial multitude of ideas a two-stage reusable VTHL design was pushed forward that eventually resulted in a reusable orbiter payload spacecraft and reusable solid rocket boosters. The external tank and the launch vehicle load frame were discarded, and the parts that were reusable took a 10,000-person group nine months to refurbish for flight. So the space shuttle ended up costing a billion dollars per flight.[5] Early studies from 1980 and 1982 proposed in-space uses for the tank to be re-used in space for various applications[1][2] but NASA never pursued those options beyond the proposal stage.
During the 1970s further VTVL and HTHL SSTO designs were proposed for solar power satellite and military applications. There was a VTVL SSTO study by Boeing. HTHL SSTO designs included the Rockwell Star-Raker and the Boeing HTHL SSTO study. However the focus of all space launch funding in the United States on the Shuttle killed off these prospects. The Soviet Union followed suit with Buran. Others preferred expendables for their lower design risk, and lower design cost.
Eventually the Shuttle was found to be expensive to maintain, even more expensive than an expendable launch system would have been. The cancellation of a Shuttle-Centaur rocket after the loss of Challenger also caused an hiatus that would make it necessary for the United States military to scramble back towards expendables to launch their payloads. Many commercial satellite customers had switched to expendables even before that, due to unresponsiveness to customer concerns by the Shuttle launch system.
In 1986 President Ronald Reagan called for an airbreathing scramjet plane to be built by the year 2000, called NASP/X-30 that would be capable of SSTO. Based on the research project copper canyon the project failed due to severe technical issues and was cancelled in 1993.
This research may have inspired the British HOTOL program, which rather than airbreathing to high hypersonic speeds as with NASP, proposed to use a precooler up to Mach 5.5. The program's funding was canceled by the British government when the research identified some technical risks as well as indicating that that particular vehicle architecture would only be able to deliver a relatively small payload size to orbit.
When the Soviet Union collapsed in the early nineties, the cost of Buran became untenable. Russia has only used pure expendables for space launch since.
The 1990s saw interest in developing new reusable vehicles. The military Strategic Defense Initiative ("Star Wars") program "Brilliant Pebbles" required low cost, rapid turnaround space launch. From this requirement came the McDonnell Douglas Delta Clipper VTVL SSTO proposal. The DC-X prototype for Delta Clipper demonstrated rapid turnaround time and that automatic computer control of such a vehicle was possible. It also demonstrated it was possible to make a reusable space launch vehicle which did not require a large standing army to maintain like the Shuttle.
In mid-1990, further British research and major reengineering to avoid deficiencies of the HOTOL design led to the far more promising Skylon design, with much greater payload.
From the commercial side, large satellite constellations such as Iridium satellite constellation were proposed which also had low cost space access demands. This fueled a private launch industry, including partially reusable vehicle players, such as Rocketplane Kistler, and reusable vehicle players such as Rotary Rocket.
The end of that decade saw the implosion of the satellite constellation market with the bankruptcy of Iridium. In turn the nascent private launch industry collapsed. The fall of the Soviet Union eventually had political ripples which led to a scaling down of ballistic missile defense, including the demise of the "Brilliant Pebbles" program. The military decided to replace their aging expendable launcher workhorses, evolved from ballistic missile technology, with the EELV program. NASA proposed riskier reusable concepts to replace Shuttle, to be demonstrated under the X-33 and X-34 programs.
The 21st century saw rising costs and teething problems lead to the cancellation of both X-33 and X-34. Then the Space Shuttle Columbia disaster and another grounding of the fleet. The Shuttle design was now over 20 years old and in need of replacement. Meanwhile, the military EELV program churned out a new generation of better expendables. The commercial satellite market is depressed due to a glut of cheap expendable rockets and there is a dearth of satellite payloads.
Against this backdrop came the Ansari X Prize contest, inspired by the aviation contests made in the early 20th century. Many private companies competed for the Ansari X Prize, the winner being Scaled Composites with their reusable HTHL SpaceShipOne. It won the ten million dollars, by reaching 100 kilometers in altitude twice in a two-week period with the equivalent of three people on board, with no more than ten percent of the non-fuel weight of the spacecraft replaced between flights. While SpaceShipOne is suborbital like the X-15, some hope the private sector can eventually develop reusable orbital vehicles given enough incentive. SpaceX is a recent player in the private launch market succeeding in converting its Falcon 9 expendable launch vehicle into a partially reusable vehicle by returning the first stage for reuse.
On 23 November 2015, Blue Origin New Shepard rocket became the first proven Vertical Take-off Vertical Landing (VTVL) rocket which can reach space, by passing Kármán line (100 kilometres), reaching 329,839 feet (100.5 kilometers). [6] Previous VTVL record was in 1994, the McDonnell Douglas DC-X ascended to an altitude of about 3.1 kilometers before successfully landing. [7]
Reusability concepts
Single stage
There are two approaches to Single stage to orbit or SSTO. The rocket equation says that an SSTO vehicle needs a high mass ratio. Mass ratio is defined as the mass of the fully fueled vehicle divided by the mass of the vehicle when empty (zero fuel weight, ZFW).One way to increase the mass ratio is to reduce the mass of the empty vehicle by using very lightweight structures and high efficiency engines. This tends to push up maintenance costs as component reliability can be impaired, and makes reuse more expensive to achieve. The margins are so small with this approach that there is uncertainty whether such a vehicle would be able to carry any payload into orbit.
Two or more stages to orbit
Two stage to orbit requires designing and building two independent vehicles and dealing with the interactions between them at launch. Usually the second stage in launch vehicle is 5-10 times smaller than the first stage, although in biamese and triamese[8] approaches each vehicle is the same size.In addition, the first stage needs to be returned to the launch site for it to be reused. This is usually proposed to be done by flying a compromise trajectory that keeps the first stage above or close to the launch site at all times, or by using small airbreathing engines to fly the vehicle back, or by recovering the first stage downrange and returning it some other way (often landing in the sea, and returning it by ship.) Most techniques involve some performance penalty; these can require the first stage to be several times larger for the same payload, although for recovery from downrange these penalties may be small.
The second stage is normally returned after flying one or more orbits and reentering.
Biamese & Triamese (Crossfeed)
Two or three similar stages are stacked side by side, and burn in parallel. Using crossfeed, the fuel tanks of the orbital stage are kept full, while the tank(s) in the booster stage(s) are used to run engines in the booster stage(s) and orbital stage. Once the boosters run dry, they are ejected, and (typically) glide back to a landing. The advantage to this is that the mass ratios of the individual stages is vastly reduced due to the way cross feed modifies the rocket equation. Isp*g*ln(2MR^2/MR+1) & Isp*g*ln(3MR^2/MR+2) respectively. With hydrogen engines, a triamese only needs an MR of 5, as opposed to an MR of 10 for a single-stage equivalent vehicle.A criticism of this approach is that designing separate orbiter and boosters, or a single vehicle that could do both, would compromise performance, safety, and possible cost savings. Compromising maximum performance to reduce cargo cost however, is the point of the triamese approach. Stacking two or three winged vehicles can also be challenging. Optimistically, the lower mass ratios would translate to lower overall R&D costs, even if two different stage designs. While many aerospace designs have successfully been modified far beyond the original designers intentions (Boeing's 747 is perhaps the best example) the slow and painful birth of the F-35 family demonstrates that it is not always a guarantee of such flexibility.
Crossfeed is to be an important part of SpaceX's Falcon Heavy - and one of the main reasons it will be able to lift over ~4 times as much cargo to orbit as the Falcon 9 v1.1.
Horizontal landing
Scaled Composites SpaceShipOne used horizontal landing after being launched from a carrier airplane
Concepts such as lifting bodies attempt to deal with the somewhat conflicting issues of reentry, hypersonic and subsonic flight; as does the delta wing shape of the Space Shuttle.
Vertical landing
McDonnell Douglas DC-X used vertical takeoff and vertical landing
Alternatively rockets could be used to softland the vehicle on the ground from the subsonic speeds reached at low altitude (see DC-X). This typically requires about 10% of the landing weight of the vehicle to be propellant.
A slightly different approach to vertical landing is to use an autogyro or helicopter rotor. This requires perhaps 2-3% of the landing weight for the rotor.
Blue Origin New Shepard rocket became the first proven rocket which can do vertical landing after reaching space,[clarification needed] by passing Kármán line (100 kilometres).[6]
SpaceX's Falcon 9 rocket became the first orbital rocket to vertically land its first stage on the ground, after propelling its second stage and payload to a suborbital trajectory, where it would continue on to orbit. <[9]
Horizontal takeoff
XCOR Aerospace EZ-Rocket used horizontal takeoff and landing using a standard airport runway
Vertical takeoff
See also: VTVL
This is the traditional takeoff regime for pure rocket vehicles.
Rockets are good for this regime, since they have a very high
thrust/weight ratio (~100).Airbreathing
Airbreathing approaches use the air during ascent for propulsion. The most commonly proposed approach is the scramjet, but turborocket, Liquid Air Cycle Engine (LACE) and precooled jet engines have also been proposed.In all cases the highest speed that an airbreathing engine can reach is far short of orbital speed (about Mach 15 for Scramjets and Mach 5-6 for the other engine designs), and rockets would be used for the remaining 10-20 Mach into orbit.
The thermal situation for airbreathers (particularly scramjets) can be awkward; normal rockets fly steep initial trajectories to avoid drag, whereas scramjets would deliberately fly through relatively thick atmosphere at high speed generating enormous heating of the airframe. The thermal situation for the other airbreathing approaches is much more benign, although is not without its challenges.
Propellant
Hydrogen fuel
Hydrogen is often proposed since it has the highest exhaust velocity. However tankage and pump weights are high due to insulation and low propellant density; and this wipes out much of the advantage.Still, the 'wet mass' of a hydrogen fuelled stage is lighter than an equivalent dense stage with the same payload and this can permit usage of wings, and is good for second stages.
Dense fuel
Dense fuel is sometimes proposed since, although it implies a heavier vehicle, the specific tankage and pump mass is much improved over hydrogen. Dense fuel is usually suggested for vertical takeoff vehicles, and is compatible with horizontal landing vehicles, since the vehicle is lighter than an equivalent hydrogen vehicle when empty of propellant. Non-cryogenic dense fuels also permit the storage of fuel in wing structures. Projects have been underway to densify existing fuel types through various techniques. These include slush technologies for cryogenics like hydrogen and propane. Another densifying method has been studied that would also increase the specific impulse of fuels. Adding finely powdered carbon, aluminum, titanium, and boron to hydrogen and kerosene have been studied. These additives increase the specific impulse (Isp) but also the density of the fuel. For instance, the French ONERA missile program tested boron with kerosene in gelled slurries, as well as embedded in paraffin, and demonstrated increases in volumetric specific impulse of between 20-100%.Tripropellant
Dense fuel is optimal early on in a flight, since the thrust to weight of the engines is better due to higher density; this means the vehicle accelerates more quickly and reaches orbit sooner, reducing gravity losses.However, for reaching orbital speed, hydrogen is a better fuel, since the high exhaust velocity and hence lower propellant mass reduces the take off weight.[citation needed]
Therefore, tripropellant vehicles[citation needed] start off burning with dense fuel and transition to hydrogen. (In a sense the Space Shuttle does this with its combination of solid rockets and main engines, but tripropellant vehicles usually carry their engines to orbit.[citation needed])
Propellant costs
As with all current launch vehicles propellant costs for a rocket are much lower than the costs of the hardware. However, for reusable vehicles if the vehicles are successful, then the hardware is reused many times and this would bring the costs of the hardware down. In addition, reusable vehicles are frequently heavier and hence less propellant efficient, so the propellant costs could start to multiply up to the point where they become significant.Launch assistance
Since rocket delta-v has a non linear relationship to mass fraction due to the rocket equation, any small reduction in delta-v gives a relatively large reduction in the required mass fraction; and starting a mission at higher altitude also helps.Many systems have proposed the use of aircraft to gain some initial velocity and altitude; either by towing, carrying or even simply refueling a vehicle at altitude.
Various other launch assists have been proposed, such as ground-based sleds, or maglev systems, high altitude (80 km) maglev systems such as launch loops, to more exotic systems such as tether propulsion systems to catch the vehicle at high altitude, or even Space Elevators.
Reentry heat shields
Main article: Atmospheric reentry
Robert Zubrin has said that as a rough rule of thumb, 15% of the landed weight of a vehicle needs to be aerobraking reentry shielding.[10]Reentry heat shields on these vehicles are often proposed to be some sort of ceramic and/or carbon-carbon heat shields, or occasionally metallic heat shields (possibly using water cooling or some sort of relatively exotic rare earth metal.)[citation needed]
Some shields would be single-use ablatives, discarded after reentry.[citation needed]
A newer Thermal Protection System (TPS) technology was first developed for use in steering fins on ICBM MIRVs. Given the need for such warheads to reenter the atmosphere swiftly and retain hypersonic velocities to sea level, researchers developed what are known as SHARP materials, typically hafnium diboride and zirconium diboride, whose thermal tolerance exceeds 3600 C. SHARP equipped vehicles can fly at Mach 11 at 30 km altitude and Mach 7 at sea level. The sharp-edged geometries permitted with these materials also eliminates plasma shock wave interference in radio communications during reentry. SHARP materials are very robust and would not require constant maintenance, as is the case with technologies like silica tiles, used on the Space Shuttle, which account for over half of that vehicles maintenance costs and turnaround time. The maintenance savings alone are thus a major factor in favor of using these materials for a reusable launch vehicle, whose raison d'etre is high flight rates for economical launch costs.[citation needed]
Weight penalty
The weight of a reusable vehicle is almost invariably higher than an expendable that was made with the same materials, for a given payload.R&D
The research & development costs of reusable vehicle are expected to be higher, because making a vehicle reusable implies making it robust enough to survive more than one use, which adds to the testing required. Increasing robustness is most easily done by adding weight; but this reduces performance and puts further pressure on the R&D to recoup this in some other way.These extra costs must be recouped; and this pushes up the average cost of the vehicle.
Maintenance
Reusable launch systems require maintenance, which is often substantial. The Space Shuttle system requires extensive refurbishing between flights, primarily dealing with the silica tile TPS and the high performance LH2/LOX burning main engines. Both systems require a significant amount of detailed inspection, rebuilding and parts replacement between flights, and account for over 75% of the maintenance costs of the Shuttle system. These costs, far in excess of what had been anticipated when the system was constructed, have cut the maximum flight rate of Shuttle to 1/4 of that planned. This has also quadrupled the cost per pound of payload to orbit, making Shuttle economically infeasible in today's launch market for any but the largest payloads, for which there is no competition.For any RLV technology to be successful, it must learn from the failings of Shuttle and overcome those failings with new technologies in the TPS and propulsion areas.
Manpower and logistics
The Space Shuttle program required a standing army of over 9,000 employees to maintain, refurbish, and relaunch the shuttle fleet, irrespective of flight rates. That manpower budget must be divided by the total number of flights per year. The fewer flights means the cost per flight goes up significantly. Streamlining the manpower requirements of any launch system is an essential part of making an RLV economical. Projects that have attempted to develop this ethic include the DC-X Delta Clipper project, as well as SpaceX's Falcon 9 and Falcon 1 programs.One issue mitigating against this drive for labor savings is government regulation. Given that NASA and USAF (as well as government programs in other countries) are the primary customers and sources of development capital, government regulatory requirements for oversight, parwork, quality, safety, and other documentation tend to inflate the operational costs of any such system.
Orbital reusable launchers
Under development
- Adeline - Reusable launch system concept developed by Airbus Defence and Space
- Avatar RLV - Under development, first scaled-down demonstration flight planned in 2015.[11][12]
- Blue Origin is developing a reusable booster system, as of November 2015.[13][7] Blue Origin New Shepard rocket is the first rocket successfully launched and which is proven to be able to land vertically on earth VTVL after reaching space, by passing Kármán line. [6]
- As of 2014, China is working on a project to recover rocket boosters, using a "paraglider-type wings" approach. Powered flight tests are in the future, and the process is expect to take until approximately 2018.[14]
- Skylon (spacecraft) (proposed airbreathing SSTO spaceplane)
- SpaceX reusable rocket launching system—(currently in development and test)—is planned for use on both the Falcon 9 and Falcon Heavy launch vehicles. A second-generation VTVL reusable design was publicly announced in 2011.[15][16] The low-altitude flight test program of an experimental technology-demonstrator launch vehicle began in 2012, with more extensive high-altitude over-water flight testing planned to begin in mid-2013, and continue on each subsequent Falcon 9 flight.[17] On December 21, 2015, SpaceX successfully landed a Falcon 9 first stage after it boosted 11 commercial satellites into low earth orbit on Falcon 9 Flight 20.[18]
- Swiss Space Systems is developing launching system including the suborbital spaceplane SOAR. The first 2 stages, an Airbus 300 and SOAR, are completely reusable.[19]
- zero2infinity is developing a launching system called bloostar based on the rockoon system, which consists in elevating to the near space the launcher using a high-altitude balloon and once there launch a multi-stage rocket to put a satellite into orbit.[20]
Proposed and concept vehicles
- Indian Space Shuttle Program
- SpaceFleet (The EARL Project - a space-capable UAV concept[when?][21][full citation needed]
- SpaceLiner (a mid-2000s German proposed suborbital, hypersonic, winged passenger transport concept)
- Shenlong (spacecraft) (an early 2000s Chinese proposed, scaled model tested at high altitude in 2005)
- PlanetSpace Silver Dart (a 2000s partially reusable spaceplane concept, based on a hypersonic glider design)
- As of January 2015, the French space agency CNES is working with Germany and a few other governments to start a modest research effort with a hope to propose a LOX/methane engine on a reusable launch vehicle by mid-2015, with flight testing unlikely before approximately 2026.[22][23]
- Sura (proposed by Ukraine)[citation needed]
- CORONA (proposed by Russia)
Historical
- Buran (partially reusable, retired)
- Space Shuttle (partially reusable, retired)
Cancelled
- Baikal French/Russian early-2000s joint-project concept. Cancelled after "CNES officials concluded that a rocket system with a reusable first stage would need to launch some 40 times a year" in order to make the project economically feasible.[23]
- HOTOL British SSTO.
- Hyperion SSTO 1960s concept HTVL spacecraft.[4]
- Kliper planned Russian partly reusable orbiter, cancelled in 2006.[citation needed]
- Liquid Fly-back Booster proposed design of reusable boosters for Ariane 5 with additional derivatives
- MAKS proposed Russian system of Buran-like smaller winged reusable orbiter on heavy aircraft carrier.
- Spiral cancelled Soviet military system of small winged reusable orbiter on winged hypersonic air-carrier.[citation needed]
- Phoenix SSTO[24]
- X-30 NASP, X-33 and VentureStar proposed SSTO replacement for the Space Shuttle, cancelled in 2001.[citation needed]
- Roton Commercial launch vehicle project, cancelled in 2000 due to lack of funds.
Reusability dropped, flown only as expendable
- SpaceX Falcon 1 was announced as a partially reusable launch vehicle, and the 28 September 2008 test flight reached orbit, but vehicle recovery was never demonstrated and the vehicle was retired after 2009.[25
MAKS (spacecraft)
From Wikipedia, the free encyclopedia
![]()
Schematic view of the MAKS space plane
|
|
Country of origin | Soviet Union |
---|---|
Operator | Soviet space program |
Applications | Transport to low Earth orbit and back |
Specifications | |
Regime | Low Earth orbit |
Production | |
Status | Canceled, 1991 |
Launched | None |
The MAKS (Multipurpose aerospace system) (Russian: МАКС (Многоцелевая авиационно-космическая система)) is a cancelled Soviet air-launched with orbiter Reusable launch system project that was proposed in 1988, but cancelled in 1991. The orbiter was supposed to reduce the cost of transporting materials to Earth orbit by a factor of ten. The reusable orbiter and its external non-reusable fuel tank, was to have been launched by an Antonov AN-225 airplane, developed by Antonov ASTC (Kyiv, Ukraine). Had it been built, the system would have weighed 275 metric tons (271 long tons; 303 short tons), and would have been capable of carrying a 7-metric-ton (6.9-long-ton; 7.7-short-ton) payload.[1]
Three variants of the MAKS system were conceived: MAKS-OS, the standard configuration; MAKS-T, with upgraded payload capability; and MAKS-M, a version that included its fuel tank within the envelope of the orbiter.[2]
As of June 2010, Russia was considering reviving the MAKS program.[3] In Ukraine this project has developed into other air-launched orbiter projects, such as Svityaz and Oril.
Reusable Military Spaceplane Tops DARPA's Budget Request, Again
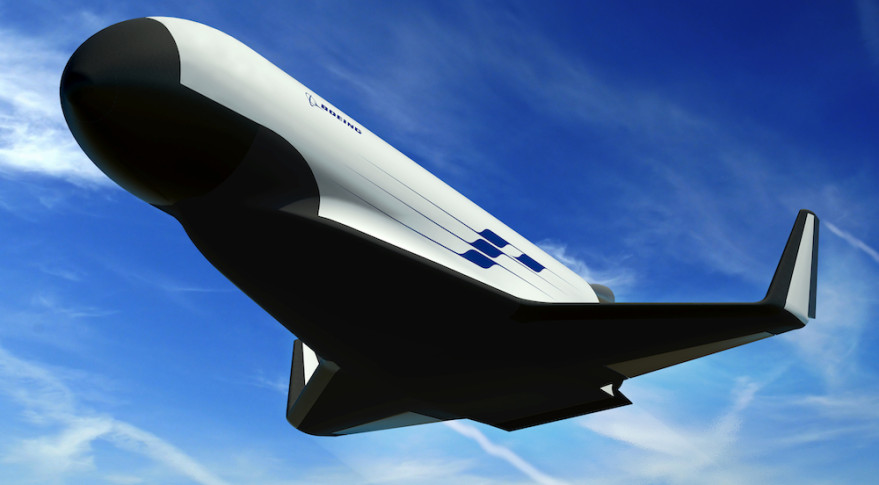
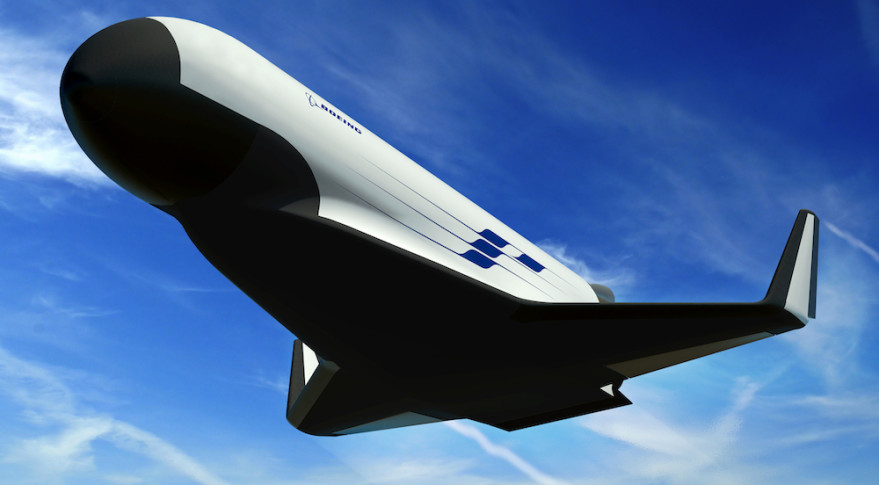
Boeing is
one of three teams designing a new spaceplane for DARPA's Experimental
Spaceplane-1 program, known as XS-1. The program leads DARPA's
space-related budget requests for fiscal year 2017.
Credit: Boeing
DARPA asked for $50 million in the Pentagon's 2017 budget request for its Experimental Spaceplane 1, or XS-1 program. That's up from a $30 million the agency asked for during the fiscal year 2016 budget cycle.
XS-1 aims to develop a reusable first stage that could carry an expendable upper stage capable of placing payloads weighing up to 1,800 kilograms into orbit. DARPA said the vehicle could ultimately fly 10 times in 10 days and boost payloads into low Earth orbit for less than $5 million per launch. [DARPA's XS-1 Military Space Plane Concept in Pictures]
Three industry teams are working on the program: Boeing and Blue Origin; Masten Space Systems and XCOR Aerospace; and Northrop Grumman and Virgin Galactic.
In July, all three teams received funding to continue design work and risk reduction activities in preparation for a production contract.
DARPA said in 2014 it intended to pick one team in 2015 to work toward demonstration flight in 2018, but now it is unclear when such a downselect will occur.
DARPA said in budget documents that it plans to complete system and subsystem designs later this year, as well as coordinate with the Federal Aviation Administration for preliminary flight test planning.
A critical design review is planned for fiscal year 2017, the documents said.
In October, the Government Accountability Office said none of several Defense Department efforts to field quick-reaction launch vehicles, including XS-1, have advanced past the development stage.
In its 2017 budget request DARPA asked for $175 million for its space programs and technology office, significantly higher than the $127 million budget for 2016.
In addition to $50 million for XS-1, next year's budget would also include:
- $45 million for the RadarNet program. an effort to design a deployable lightweight, low-power and wideband-capable communications antenna for cubesats.
- $33 million for Robotic Servicing of Geostationary Satellites, which would establish a robotics operation in geosynchronous orbit to perform servicing tasks.
Reusable Military Spaceplane Tops DARPA's Budget Request, Again
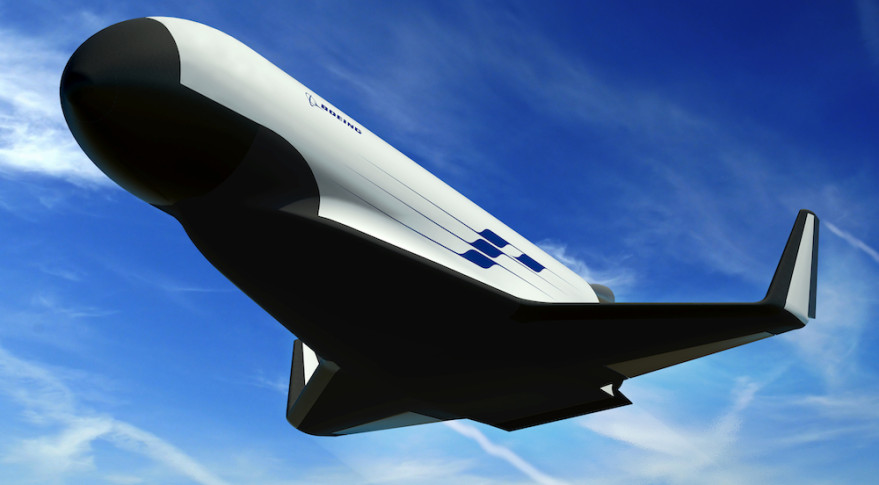
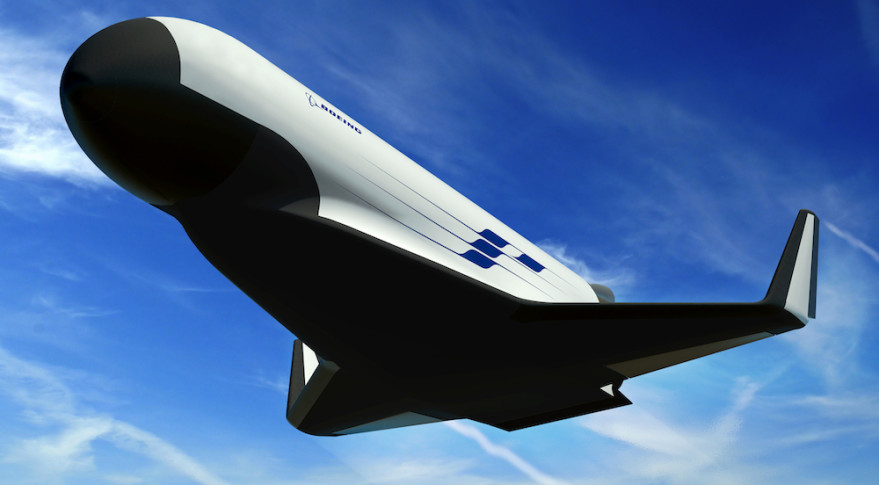
Boeing is
one of three teams designing a new spaceplane for DARPA's Experimental
Spaceplane-1 program, known as XS-1. The program leads DARPA's
space-related budget requests for fiscal year 2017.
Credit: Boeing
DARPA asked for $50 million in the Pentagon's 2017 budget request for its Experimental Spaceplane 1, or XS-1 program. That's up from a $30 million the agency asked for during the fiscal year 2016 budget cycle.
XS-1 aims to develop a reusable first stage that could carry an expendable upper stage capable of placing payloads weighing up to 1,800 kilograms into orbit. DARPA said the vehicle could ultimately fly 10 times in 10 days and boost payloads into low Earth orbit for less than $5 million per launch. [DARPA's XS-1 Military Space Plane Concept in Pictures]
Three industry teams are working on the program: Boeing and Blue Origin; Masten Space Systems and XCOR Aerospace; and Northrop Grumman and Virgin Galactic.
In July, all three teams received funding to continue design work and risk reduction activities in preparation for a production contract.
DARPA said in 2014 it intended to pick one team in 2015 to work toward demonstration flight in 2018, but now it is unclear when such a downselect will occur.
DARPA said in budget documents that it plans to complete system and subsystem designs later this year, as well as coordinate with the Federal Aviation Administration for preliminary flight test planning.
A critical design review is planned for fiscal year 2017, the documents said.
In October, the Government Accountability Office said none of several Defense Department efforts to field quick-reaction launch vehicles, including XS-1, have advanced past the development stage.
In its 2017 budget request DARPA asked for $175 million for its space programs and technology office, significantly higher than the $127 million budget for 2016.
In addition to $50 million for XS-1, next year's budget would also include:
- $45 million for the RadarNet program. an effort to design a deployable lightweight, low-power and wideband-capable communications antenna for cubesats.
- $33 million for Robotic Servicing of Geostationary Satellites, which would establish a robotics operation in geosynchronous orbit to perform servicing tasks.
No comments:
Post a Comment